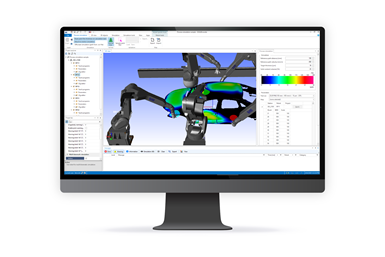
Dürr’s newly developed simulation software is said to allow car manufacturers to reduce the number of real-life tests. Photo Credit: Dürr
Uniform layer thicknesses are an important quality factor in industrial car painting. Typically, numerous test runs are necessary when launching new models to ensure the perfect painting results are achieved. Dürr Systems Inc. (Southfield, Mich.) has announced a new solution for digital paint layer calculation.
The company has succeeded in calculating layer thicknesses virtually, and is incorporating this module into the existing programming software for application robots. According to Dürr, with the newly developed simulation software, car manufacturers can reduce the number of real-life tests.
Whenever there is a new project in a paint shop, precise adjustments are needed until the applied paint meets the required layer thickness everywhere on the body. Until everything is properly adjusted, bodies undergo test painting in a complex parameterization process. Dürr claims its new simulation allows manufacturers to model and optimize this process virtually.
“It is now possible to reduce the number of test paint runs and test bodies by more than 50%,” explains Dr. Lars Friedrich, president & CEO Application Technology at Dürr Systems AG. “This makes commissioning more efficient, lowers material costs, and results in fewer poorly coated bodies.”
The overall objective of the simulation is to make the painting process more economical with computer-assisted product and process developments from end to end, while delivering the same top quality. Simulations can help even before the first vehicle prototypes get as far as production. Using qualified calculations, they anticipate where any problems might occur and provide remedies prior to manufacturing. In terms of the layer thickness, this also includes complex body parts that are challenging to paint — joints in the trunk, for example.
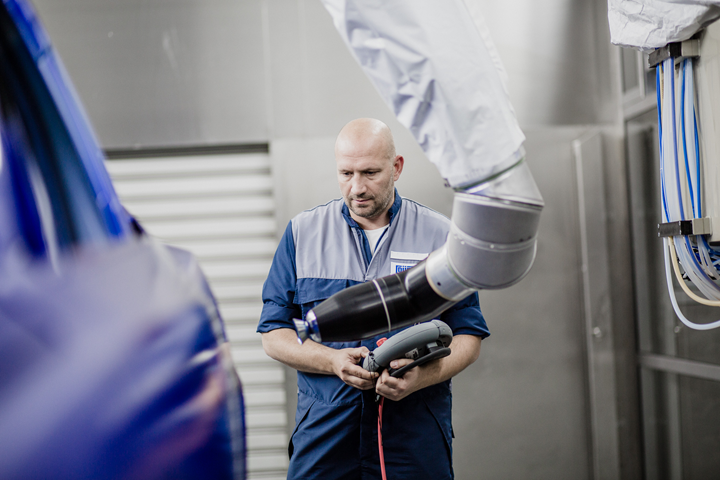
Real-life results from the Dürr test laboratory are incorporated into the simulation program. Photo Credit: Dürr
How the simulation software works
The new DXQ3D.onsite module is based on a three-step concept. The first step consists of a virtual calculation of how much paint is applied at any point. The software runs its simulations exclusively using idealized, virtual spray patterns based closely on actual conditions. The spray patterns can be scaled dynamically in height and with different widths. The user can experiment with these two parameters to estimate and visualize what general effect different spray pattern widths and percentage discharge rates will have on the layer thickness distribution.
To model the reality in advance on the computer, the software module creates a digital twin of all key individual components in the form of electronic data. During the first simulation, the tool automatically converts the uploaded file formats into its own 3D file format of the body. This keeps all the necessary additional data ready and, at the same time, removes data of no significance for the painting operation. This has the effect of reducing the storage space required as well as the calculating time so that the program can also be used on a notebook directly at the spray booth in production. Once all the relevant data is merged for the final time, a virtual spray pattern along the robot paths programmed off-site is produced. It adds up the layer thicknesses and displays them in a 3D paint map. This enables different optimization solutions to be visualized in a transparent way, considered by the team and improved upon prior to production.
The software simulations do not take into account specific paints. For that reason, the process simulation concept includes a real-life test in the Dürr test laboratory as a second step after the virtual optimization. The customers’ chosen paint materials are used in this test. The values measured are used in the third and last step to translate the virtual parameters used in the simulation, such as spray pattern width and percentage discharge rate, into parameters for the paint atomizer. The real-life results are incorporated into the simulation program during this “translation.” As soon as the map is imported, the software automatically suggests atomizer parameters. The first real-life test painting of a body is then carried out with this set of pre-optimized parameters.
The software module’s short calculating times make it possible to simulate the paint layer thicknesses of complete bodies and estimate the quality within a few minutes on a conventional PC, not a mainframe computer. “This makes it easy to assess the quality of paint layer thicknesses, better interpret coating results and optimize neuralgic zones with inconsistent layer thicknesses,” says Frank Herre, head of Application Process Development at Dürr Systems AG.
The process simulation is available as an additional module to the DXQ3D.onsite standard software included with every Dürr painting robot. DXQ3D.onsite is the digital universal tool that can be used to program motion paths using realistic simulations of all robots at a station or to parameterize application processes.
Related Content
NASF/AESF Foundation Research Project #121: Development of a Sustainability Metrics System and a Technical Solution Method for Sustainable Metal Finishing - 12th Quarterly Report
This NASF-AESF Foundation research project report covers the twelfth quarter of project work (January-March 2023) at Wayne State University in Detroit. In this period, our main effort concentrated on documenting technical content that was yet to be reported, including analysis of costs for specific technologies for sustainability improvement.
Read MoreShedding Light on Surface Inspection
State-of-the-art reflector-based lighting system improves luminosity and ergonomics for surface inspection tasks while reducing energy usage.
Read MorePowder Coating Overcomes Post Forming
Six Sigma methodology, open communication, and collaboration produce results for leading boat manufacturer.
Read MoreSUR/FIN 2023: Capsules from the Technical Sessions I: Emerging Technologies
SUR/FIN 2023 in Cleveland this past June was a resounding success. Due to the efforts of the Technical Activities Committee, ably led by Bill Nebiolo this year, an outstanding program of technical presentations was offered. What follows are summaries of selected presentations from the Emerging Technologies sessions. Additional coverage will be provided in this space in the coming months. The full report can be accessed and printed at short.pfonline.com/NASF23Aug1.
Read MoreRead Next
Sports Car Manufacturer Embraces Automation with Dürr
Lotus is using technology from Dürr, including painting robots, updated painting supply systems and a new drying rack, to modernize its paint shop.
Read MoreCompact Painting Robot Enables Innovative Paint Systems
WB Coatings has invested in the Dürr ready2spray robot to develop chrome-effect paint systems consisting of reproducible coating layers of 2 to 3 µm.
Read MorePaint Booth of the Future Concept from Dürr
Dürr’s EcoProBooth has a modular box design, combines interior and exterior painting in one box and is designed for flexibility.
Read More