NASF/AESF Foundation Research Project #121: Development of a Sustainability Metrics System and a Technical Solution Method for Sustainable Metal Finishing - 12th Quarterly Report
This NASF-AESF Foundation research project report covers the twelfth quarter of project work (January-March 2023) at Wayne State University in Detroit. In this period, our main effort concentrated on documenting technical content that was yet to be reported, including analysis of costs for specific technologies for sustainability improvement.
Yinlun Huang*
Department of Chemical Engineering and Materials Science
Wayne State University
Detroit, Michigan, USA
Editor’s Note: This NASF-AESF Foundation research project report covers the twelfth quarter of project work (January-March 2023) at Wayne State University in Detroit. A printable PDF version of this report is available by clicking HERE.
It is widely recognized in many industries that sustainability is a key driver of innovation. Numerous companies, especially large ones who made sustainability as a goal, are achieving clearly more competitive advantages. The metal finishing industry, however, is clearly behind others in response to the challenging needs for sustainable development.
This research project aims to:
- Create a metal-finishing-specific sustainability metrics system, which will contain sets of indicators for measuring economic, environmental and social sustainability,
- Develop a general and effective method for systematic sustainability assessment of any metal finishing facility that could have multiple production lines, and for estimating the capacities of technologies for sustainability performance improvement,
- Develop a sustainability-oriented strategy analysis method that can be used to analyze sustainability assessment results, identify and rank weaknesses in the economic, environmental, and social categories, and then evaluate technical options for performance improvement and profitability assurance in plants, and
- Introduce the sustainability metrics system and methods for sustainability assessment and strategic analysis to the industry.
This will help metal finishing facilities to conduct a self-managed sustainability assessment as well as identify technical solutions for sustainability performance improvement.
1. Student participation
Abdurrafay Siddiqui, a PhD student in the PI’s group, conducted research on this project in this reporting period. The student is financially supported mainly by Wayne State University’s Graduate Teaching Assistantship Program, and partially by this AESF research project.
2. Project activities and progress
In this reporting period, our main activities are summarized as follows: (i) generation of a manuscript for journal publication, and (ii) paper preparation for conferences.
2.1. Generation of a manuscript for journal publication.
We submitted a manuscript to J. of Cleaner Production (Impact Factor: 11.07) for publication on March 15, 2023. The manuscript is authored by Abdurrafay Siddiqui (graduate student), Rebecca Potoff (undergraduate student), and Yinlun Huang, and the title is “Sustainability Metrics and Technical Solution Derivation for Performance Improvement of Electroplating Facilities.” The abstract follows below:
The electroplating industry has been highly environmentally regulated due to the use of a variety of hazardous or toxic chemicals and waste generation in various forms within and out of the workplace. Electroplating facilities, mostly small and medium-sized, are also operated at a low profit margin. Thus, helping the facilities develop effective strategies for sustainable development becomes a focal point in the industry. In this paper, we introduce a sustainability metrics system specifically designed for the assessment of electroplating systems of any type and any production capacity. Using the metrics system, we formulate the sustainability assessment process and introduce a systematic assessment method for evaluating the sustainability performance of facilities and technology candidates, and a holistic solution method for identifying optimal technologies for the system’s sustainability performance improvement. The methodological efficacy is demonstrated through a case study on five electroplating facilities.
The manuscript contains some technical content that was either only partially reported or never reported in the previous quarterly reports. That content is summarized below.
2.1(a) Evaluation of the sustainability status of five electroplating plants before consideration for improvement.
As we have noted in earlier reports, five facilities having different production capacities were evaluated, using a number of sustainability indicators. The assessment results are summarized in Table 1, where interval numbers are shown in order to accommodate data uncertainty.
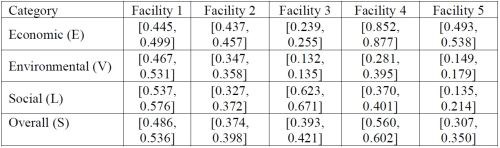
Table 1 - Categorized and overall sustainability status of five facilities before improvement steps.
2.1(b) Sustainability goal setting and budget commitment.
After reviewing the assessment results shown in Table 1, it was assumed that each facility planned to improve its sustainability performance in the economic, environmental and social sustainability categories, and commit a certain amount of funds for performance improvement. These are summarized in Table 2.
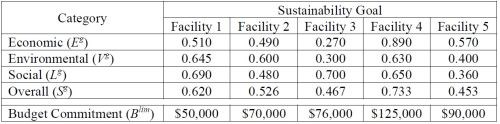
Table 2 - Sustainability goal and budget commitment set independently by the five facilities.
2.1(c) Technologies for performance improvement.
There exist many technologies for performance improvement. In the case study, three technologies were considered for possible adoption by different plants. They are:
- Technology 1 (T1): a chemical use reduction technology, which modifies the cleaning-rinsing system to directly recycle chemical solvent from a static rinsing unit to a cleaning unit while maintaining cleaning quality;
- Technology 2 (T2) – a water reuse technology, which implements a direct water reuse network with a plating line while guaranteeing rinsing quality and
- Technology 3 (T3) – an environmentally benign hoist scheduling technology, which optimizes production while reducing waste streams from a plating line.
The data for these technologies was collected from our previous studies. Table 3 shows the assessment results of the performance improvement capacity of each technology set (including individual technologies or their combinations) using the same sustainability indicators as those used for the assessment of the facilities. Again, the assessment results are also expressed as interval numbers. The cost for adopting each technology set is also indicated in the table.
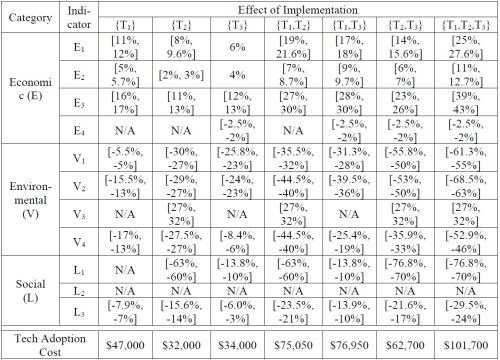
Table 3 - Effect of technology sets on individual indicators and adoption cost.
2.1(d) Technical solution identification for sustainability goal achievement.
The technical solution identification method previously reported was used to identify technologies for each facility to achieve its present sustainability goal, under the budget limit set by the facility. The identified solutions are summarized in Table 4. As shown, among those recommended technology sets, the use of T2 and T3 together offers the best performance, satisfying the sustainability goals of Facilities 2, 3 and 5. It also shows that, for Facilities 1 3, and 5, each of them has two to three options for technology adoption. As expected, the technologies improve the environmental sustainability more than the economic and social sustainability. This is because all three individual technologies (i.e., T1, T2 and T3) are mainly environmental technologies, with some added contribution to performance improvement in the other two categories. However, if other technologies had been used, such as those that focus on improving the economic and social sustainability performances, the solution identification methodology proposed in this work would be just as effective in completing the technology evaluation in a systematic way.
Note that the same technical solution used by different facilities may give different levels of performance improvement if the facilities’ original sustainability statuses are different. It is understandable that a technology may contribute more in performance improvement if a facility’s original performance is poor. The technology may not be as useful if a facility’s performance is already very good. As shown in table, the use of T1 and T2 together helps Facility 5 the most in performance improvement, Facility 3 the second most, and Facility 1 the least. This is because the environmental and social sustainability performance of Facility 5 is rather poor, and the economic and environmental sustainability performance of Facility 3 is poorer than that of Facility 1. To help visualize the solution’s sustainability performance improvement capacities in different sustainability categories for different facilities, we generated a bar chart, shown in Fig. 1.

Table 4 - Summary of technology selection results for the five facilities.
(*) The original funds committed by Facility 1 (F1) ($50,000) were insufficient for adopting any technology for performance improvement. The facility then agreed to increase the budget to $80,000.
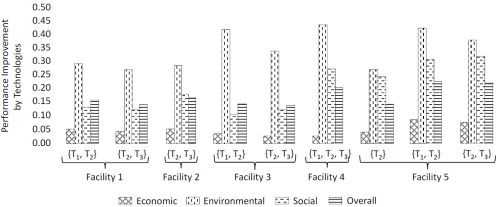
Figure 1 - Sustainability performance improvement by technologies in different facilities.
2.1(e) Profitability study.
Table 4 shows the effects of the technology sets after implementation in different facilities. It is convenient for them to evaluate their profitability gains after adopting the recommended technologies. For instance, Facility 5 saw a major improvement in economic sustainability after implementing the technology sets (T1 and T2). Here we take a range of $10,000,000 to $11,000,000 as the yearly pre-tax revenue to understand the effects of the technology on the profit of the facility over 10 years. We also take a maintenance cost of $2,500 every three years for the use of the technologies. The technology will be paid off in three years with equal payments. From the net present values of Facility 5 with and without the technology, seen in Fig. 2, it becomes clear that Facility 5 with the technology set always has a better net present value than the facility without it. For the first three years, the difference is low and for the third year, when maintenance is required, the difference between the net present values seems to plateau for one year. However, after that, the payments for the technology are finished and the difference continues to increase linearly. By the 10th year, the facility using the tech set has a net present value of $1,430,826. In contrast, the facility without the tech set shows a net present value of $1,204,103. This is a $226,723 return after 10 years (an average of $22,672 per year), alongside significantly lowering the amount of waste produced, water used and the product defect rate.
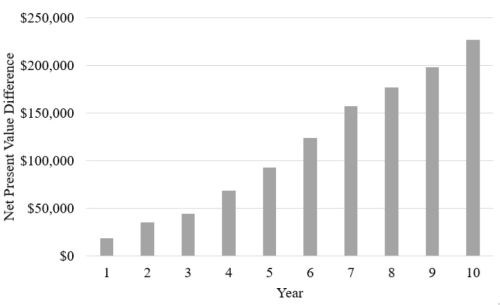
Figure 2 - Profitability improvement for Facility 5 after implementing techs T1 and T2.
2.2. Paper preparation for conferences
2.2 (a) The PI’s invited lecture.
On March 10, 2023, the PI was invited by AIChE’s Process Development Division to give a lecture at an AIChE Live Webinar, entitled “Technology Development and Assessment for Smart and Sustainable Manufacturing: A Multiscale Systems Engineering Approach.” The lecture, which was well received by the audience, included some of the results for sustainable surface finishing. The abstract follows below:
According to the National Science & Technology Council on the “Strategy for American Leadership in Advanced Manufacturing,” the next generation of technological competition in manufacturing is dictated by inventions. Although emerging technologies can become an engine of change and progress, the net profit brought to the society could be questionable if sustainability principles are not fully incorporated into technology development and application phases. It is imperative that more fundamental knowledge, systematic methodologies and powerful tools be developed to reshape technology innovations and meet industrial sustainable development goals.
Today, industries are in the midst of a significant, compelling smart transformation largely impacted by Industry 4.0, which is mainly featured by digitalization. This provides a variety of opportunities for advancing the innovation of smart and sustainable technologies.
In this presentation, we will introduce a systematic methodology for conducting comprehensive sustainability assessment of emerging technologies in their early development phase and identifying optimal technology sets for smart and sustainable manufacturing in different life-cycle stages. This methodology is developed by resorting to sustainability science, multiscale systems science and digital-twin technologies. To demonstrate methodological efficacy, we will present a number of case studies, including the assessment of technologies for smart and sustainable nanopaint design and nanocoating manufacturing, plant-wide electroplating, and heat-integrated work exchanger network design for thermal and mechanical energy recovery. Future directions for smart and sustainable manufacturing will also be discussed.
2.2(b) Papers to be presented by the students at the SUR/FIN 2023, Cleveland, OH, June 6-8, 2023.
The titles and paper abstracts are shown below:
- A. Siddiqui and Y. Huang, “Industrial Sustainability Assessment and Enhancement (ISAE) Tool.”
Technologies are a catalyst for sustainability improvement as they can help lower natural resource usage and waste production. The surface finishing industry has shown much growth over the past few years related to technological improvement and implementation. However, due to the high levels of environmental regulation, health risks and low profit margins, applying new technologies could be a risk. If sustainability principles are not thoroughly implemented and used in the assessment of new technologies, unexpected, and possibly harmful, results may ensue. However, it is also of note that technology assessments can be intensive and require large amounts of resources. Thus, it is important to not only have a sustainable technology assessment methodology, but also be able to apply this methodology easily.
In the past two years, we developed a metal-finishing-specific sustainability metrics system, which was composed of three sets of indicators for measuring over forty aspects of sustainability in economic, environmental and social dimensions. We then introduced a technology evaluation methodology that was scientific and systematic and incorporated said sustainability metrics system. In this presentation, we introduce a sustainability assessment and technology evaluation tool. This tool can be used to evaluate the sustainability performance of electroplating facilities, portray results in an easy to read manner as to facilitate future plans of action, and include technology evaluation to identify the best possible results. The capabilities of this tool will be shown through case studies by studying the sustainability of different electroplating facilities and the effects of implementing identified technologies.
- M. Moghadasi and Y. Huang, “Digital Twin-Based Dynamic Sustainability Assessment of Electroplating Facilities.”
The rapid growth of digital technologies provides a variety of opportunities for smart manufacturing. Digital Twin (DT) is one of them. Digital twins are used across the whole manufacturing lifecycle, from design to operation of manufacturing facilities. A DT is a virtual representation of a physical system, where real-time data is used to ensure its accuracy and fidelity. As manufacturing sustainability heavily relies on the availability of system information, the DT technology is naturally highly valuable for pursuing a few key tasks in sustainability, including sustainability assessment and analysis, future trend prediction, short-to-long-term strategy development for sustainability performance, and effectiveness evaluation of strategy implementation.
In this presentation, a DT-based methodology for constructing a virtual electroplating plant and performing dynamic sustainability assessment is introduced. Techniques for acquisition and utilization of dynamic data in various operational scenarios are discussed to ensure DT fidelity. A case study on zinc alloy plating is selected for using the DT platform to conduct sustainability performance evaluation using the sustainability metrics system that we have developed specifically for the metal finishing industry. The advantage of DT-based dynamic sustainability assessment is described after comparing it with conventional sustainability assessment.
2.2(c) Abstracts submitted for presentation at the AIChE Annual National Meeting, Orlando, FL, Nov. 5 - 10, 2023.
Two electroplating-related abstracts have been submitted for presentation at the AIChE Meeting. The titles are: (i) “Dynamic Sustainability Assessment in the Digital Age” and (ii) “Fuzzy Decision-Making for Sustainability Performance Improvement of Complex Systems.” Both abstracts were authored by A. Siddiqui and the PI (Y. Huang).
3. Plan for the 13th quarter of the project
Next quarter, we will be working on the Matlab based tool, ISAE. The tool will be used to conduct more case studies. Also, we plan to report our research progress on the digital twinning for sustainable metal finishing through developing digital models for characterizing the sustainability performance of electroplating systems.
4. Past project reports
1. Quarter 1 (April-June 2020): Summary: NASF Report in Products Finishing; NASF Surface Technology White Papers, 84 (12), 14 (September 2020); Full paper: http://short.pfonline.com/NASF20Sep1
2. Quarter 2 (July-September 2020): Summary: NASF Report in Products Finishing; NASF Surface Technology White Papers, 85 (3), 13 (December 2020); Full paper: http://short.pfonline.com/NASF20Dec1
3. Quarter 3 (October-December 2020): Summary: NASF Report in Products Finishing; NASF Surface Technology White Papers, 85 (7), 9 (April 2021); Full paper: http://short.pfonline.com/NASF21Apr1.
4. Quarter 4 (January-March 2021): Summary: NASF Report in Products Finishing; NASF Surface Technology White Papers, 85 (11), 13 (August 2021); Full paper: http://short.pfonline.com/NASF21Aug1.
5. Quarter 5 (April-June 2021): Summary: NASF Report in Products Finishing; NASF Surface Technology White Papers, 86 (1), 19 (October 2021); Full paper: http://short.pfonline.com/NASF21Oct2
6. Quarter 6 (July-September 2021): Summary: NASF Report in Products Finishing; NASF Surface Technology White Papers, 86 (4), 19 (January 2022); Full paper: http://short.pfonline.com/NASF22Jan3
7. Quarter 7 (October-December 2021): Summary: NASF Report in Products Finishing; NASF Surface Technology White Papers, 86 (7), 17 (April 2022); Full paper: http://short.pfonline.com/NASF22Apr2
8. Quarter 8 (January-March 2022): Summary: NASF Report in Products Finishing; NASF Surface Technology White Papers, 86 (10), 17 (July 2022); Full paper: http://short.pfonline.com/NASF22Jul2
9. Quarter 9 (April-June 2022): Summary: NASF Report in Products Finishing; NASF Surface Technology White Papers, 87 (1), 17 (October 2022); Full paper: http://short.pfonline.com/NASF22Oct1
10. Quarter 10 (July-September 2022): Summary: NASF Report in Products Finishing; NASF Surface Technology White Papers, 87 (4), 17 (January 2023); Full paper: http://short.pfonline.com/NASF23Jan2
11. Quarter 11 (October-December 2022): Summary: NASF Report in Products Finishing; NASF Surface Technology White Papers, 87 (6), 19 (March 2023); Full paper: http://short.pfonline.com/NASF23Mar1
5. About the principal investigator (PI)
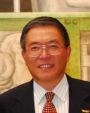
Dr. Yinlun Huang is a Professor at Wayne State University (Detroit, Michigan) in the Department of Chemical Engineering and Materials Science. He is Director of the Laboratory for Multiscale Complex Systems Science and Engineering, the Chemical Engineering and Materials Science Graduate Programs and the Sustainable Engineering Graduate Certificate Program, in the College of Engineering. He has ably mentored many students, both Graduate and Undergraduate, during his work at Wayne State.
He holds a Bachelor of Science degree (1982) from Zhejiang University (Hangzhou, Zhejiang Province, China), and M.S. (1988) and Ph.D. (1992) degrees from Kansas State University (Manhattan, Kansas). He then joined the University of Texas at Austin as a postdoctoral research fellow (1992). In 1993, he joined Wayne State University as Assistant Professor, eventually becoming Full Professor from 2002 to the present. He has authored or co-authored over 220 publications since 1988, a number of which have been the recipient of awards over the years.
His research interests include multiscale complex systems; sustainability science; integrated material, product and process design and manufacturing; computational multifunctional nano-material development and manufacturing; and multiscale information processing and computational methods.
He has served in many editorial capacities on various journals, as Co-Editor of the ASTM Journal of Smart and Sustainable Manufacturing Systems, Associate Editor of Frontiers in Chemical Engineering, Guest Editor or member of the Editorial Board, including the ACS Sustainable Chemistry and Engineering, Chinese Journal of Chemical Engineering, the Journal of Clean Technologies and Environmental Policy, the Journal of Nano Energy and Power Research. In particular, he was a member of the Editorial Board of the AESF-published Journal of Applied Surface Finishing during the years of its publication (2006-2008).
He has served the AESF and NASF in many capacities, including the AESF Board of Directors during the transition period from the AESF to the NASF. He served as Board of Directors liaison to the AESF Research Board and was a member of the AESF Research and Publications Boards, as well as the Pollution Prevention Committee. With the NASF, he served as a member of the Board of Trustees of the AESF Foundation. He has also been active in the American Chemical Society (ACS) and the American Institute of Chemical Engineers (AIChE).
He was the 2013 Recipient of the NASF William Blum Scientific Achievement Award and delivered the William Blum Memorial Lecture at SUR/FIN 2014 in Cleveland, Ohio. He was elected AIChE Fellow in 2014 and NASF Fellow in 2017. He was a Fulbright Scholar in 2008 and has been a Visiting Professor at many institutions, including the Technical University of Berlin and Tsinghua University in China. His many other awards include the AIChE Research Excellence in Sustainable Engineering Award (2010), AIChE Sustainable Engineering Education Award (2016), the Michigan Green Chemistry Governor’s Award (2009) and several awards for teaching and graduate mentoring from Wayne State University, and Wayne State University’s Charles H. Gershenson Distinguished Faculty Fellow Award.
* Dr. Yinlun Huang, Professor
Dept. of Chemical Engineering and Materials Science
Wayne State University
Detroit, MI 48202
Office: (313) 577-3771
E-mail: yhuang@wayne.edu
Related Content
Plating, Anodizing Equipment for Variety of Applications
Titan Metal Fabricators Titan Metal Fabricators, Rightech Fabrications and Optimum Anode Technologies are leading suppliers of equipment for the plating and anodizing industries.
Read MoreSUR/FIN 2023: Capsules from the Technical Sessions I: Emerging Technologies
SUR/FIN 2023 in Cleveland this past June was a resounding success. Due to the efforts of the Technical Activities Committee, ably led by Bill Nebiolo this year, an outstanding program of technical presentations was offered. What follows are summaries of selected presentations from the Emerging Technologies sessions. Additional coverage will be provided in this space in the coming months. The full report can be accessed and printed at short.pfonline.com/NASF23Aug1.
Read MoreSUR/FIN 2023 Registration Is Now Open
The National Association for Surface Finishing SUR/FIN 2023 surface finishing industry trade show will take place June 6-8, 2023 in Cleveland, Ohio.
Read MoreConnect, Collaborate and Contribute to the Industry at SUR/FIN 2024
Atlanta, Georgia, is the home to this year’s NASF SUR/FIN conference and trade show.
Read MoreRead Next
Episode 45: An Interview with Chandler Mancuso, MacDermid Envio Solutions
Chandler Mancuso, technical director with MacDermid Envio discusses updating your wastewater treatment system and implementing materials recycling solutions to increase efficiencies, control costs and reduce environmental impact.
Read MoreA ‘Clean’ Agenda Offers Unique Presentations in Chicago
The 2024 Parts Cleaning Conference, co-located with the International Manufacturing Technology Show, includes presentations by several speakers who are new to the conference and topics that have not been covered in past editions of this event.
Read MoreEducation Bringing Cleaning to Machining
Debuting new speakers and cleaning technology content during this half-day workshop co-located with IMTS 2024.
Read More