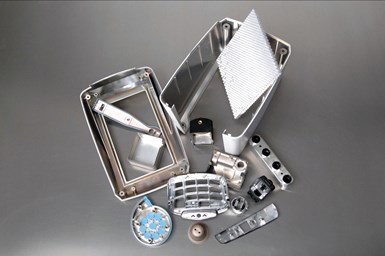
Mueller Corp. has more than 60 years of experience providing medical device manufacturers with coating solutions and services for a wide variety of applications.
Photo Credit: Mueller Corp.
Founded in 1955, Mueller Corp. (East Bridgewater, Mass.) is a third-generation, family-owned provider of vacuum metalized and industrial coatings. The company uses UV metalizing — a process that combines liquid spray and vacuum deposition — to achieve a wide variety of finishes. The process comprises a UV-cured primer, followed by a vacuum deposition layer and then finished with a UV topcoat. According to Mueller Corp., UV metalizing offers a more durable alternative to chrome plated plastic. In addition to metalizing services, the company offers a variety of liquid spray-painting services, utilizing conventional thermal and UV cure coatings.
The company serves a broad range of industries, including medical, defense, automotive, electronics and consumer. Mueller Corp. owner and president, Glenn Mueller, says that work for the medical industry accounts for 35-40% of the company’s business — and that portion is growing.
Mueller says that much of the company’s work for the medical sector involves electromagnetic interference (EMI) and radio frequency interference (RFI) shielding electronic devices used in hospitals including defibrillators, ventilators, dialysis machines and monitoring equipment. “Specific to the medical field, right now, the main coating solutions we provide are vacuum metalizing or vapor deposition — as well as spray coatings — for EMI/RFI shielding. We also do conductive painting and offer ceramic coating,” Mueller says. “Basically any hospital device that you can think of, particularly monitoring equipment, that would traditionally be made of metal, but is now made of plastic — we apply a metal coating on the inside to provide shielding.”
In addition, the company provides metalized coatings for reflectors for operating room lights and UV sterilization lights.
Like everyone else, Mueller Corp. saw a dip in business in the midst of 2020 — a year hamstrung by the COVID pandemic. And like many, the company experienced a reduction in its aerospace business. The company was able to offset some of its declining business with an increase in work for the medical sector.
Yet, Mueller points out that this wasn’t new business. The company had numerous mature programs serving the medical sector well before COVID, including the launch of a large ventilator program that was expedited by the pandemic response, but has since leveled out.
In fact, Mueller Corp. has more than 60 years of experience providing medical device manufacturers with coating solutions and services for a wide variety of applications.
Fluoropolymer coatings
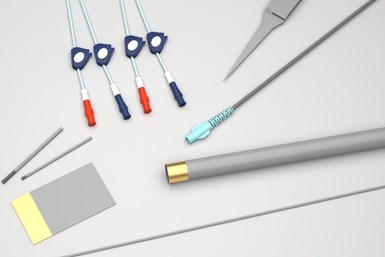
Mueller Corp. announced updates to its suite of functional coatings to include fluoropolymer coatings, including polytetrafluoroethylene (PTFE), ethylene tetrafluoroethylene (ETFE), fluorinated ethylene propylene (FEP) and perflouroalkoxy (PFA). The new products will allow the company to broaden its offerings to the medical sector.
Photo Credit: Mueller Corp.
While much of Mueller Corp.’s work is based on vacuum deposition and painted finishes, it continues to broaden its capabilities. The company places an emphasis on research and development of new coatings and continual improvement of its processes through emerging technologies and applications. In November, the company announced updates to its suite of functional coatings to include fluoropolymer coatings including polytetrafluoroethylene (PTFE), ethylene tetrafluoroethylene (ETFE), fluorinated ethylene propylene (FEP) and perflouroalkoxy (PFA).
With ISO, ASD and ITAR certifications, the company is fully equipped to support clients with functional PTFE coatings for a variety of applications. Mueller Corp. says its updated suite of industrial coatings will be largely used for projects pertaining to medical manufacturing and medical devices, but also the aerospace and defense industries.
“We’ve had the capability for a long time,” Mueller says. “We’ve done small projects, but haven’t put a focus on that space until now.”
In terms of capabilities, the technology used for spray application of fluoropolymer coatings is the same that’s used for liquid coatings. Mueller Corp. has both manual and automated high volume low pressure (HVLP) spray capabilities, including a high volume automated paint line for spray coatings. The company also has a large array of ovens for handling the different temperature requirements necessary for curing different coatings.
Mueller says putting the focus on fluoropolymer coatings will allow the company to further broaden its offerings to the medical sector. “The medical industry uses PTFE for a variety of things, mainly lubricity, but also chemical resistance, heat resistance, insulation properties,” he says.
Polytetrafluoroethylene (PTFE) is a synthetic polymer consisting of carbon and fluorine, and is designed to withstand high temperatures, water and chemicals in addition to providing a low coefficient of friction. PTFE can be used in commercial applications of industrial coatings to optimize the quality and performance of medical products and aerospace/defense products. PTFE industrial coatings are nonstick — the coatings generally lower the coefficient of friction to a range of 0.05–0.20, depending on the load, sliding speed and type of coating used.
In terms of heat resistance, PTFE industrial coatings can operate continuously at temperatures up to 500°F, and can be used for intermittent service up to 550°F with adequate ventilation without affecting any other properties. In addition, PTFE offers cryogenic stability and oftentimes can withstand temperatures as low as -454°F without loss of physical properties.
PTFE coatings also offer chemical resistance; the only chemicals known to affect these coatings are molten alkali metals and highly reactive fluorinating agents. The coatings’ low porosity leads to good permeation resistance. PTFE industrial coatings are both hydrophobic and oleophobic, meaning that the low surface energy of the coatings makes water bead up and keeps it from spreading across the surface.
The coatings also offer unique electrical properties. Over a wide range of frequencies, PTFE industrial coatings have a high dielectric strength, low dissipation factor and high surface resistivity. Adding fillers to certain PTFE coatings can make them electro-conductive enough to be used as an anti-static coating.
Finally, PTFE industrial coatings are abrasion resistant due to their excellent durability and toughness.
A natural area for growth
Mueller talks about the addition of fluoropolymer coatings to its products as a natural extension of his company’s capabilities. In essence, the company is thinking less about the immediacy of the effects of COVID on its business and instead focusing on the markets it already serves and broadening areas of expertise to explore ways to further serve those markets. Perhaps, that’s a lesson for us all.
When asked about business areas that may have helped the company make up any lost revenue during the pandemic, Mueller laughs, “Well, we also do a lot of decorative coatings for the spirits (alcohol) industry — that business doubled.”
Related Content
Replacing Discontinued Vapor Degreasing Fluids – 3 Things to Consider
What do you do when you learn your trusted line of vapor degreasing cleaning fluids will soon be discontinued? Elizabeth Norwood of MicroCare discusses what you should keep in mind when replacing discontinued vapor degreasing fluids.
Read MoreTop Shop Emphasizes Dedication, Work Ethic
With a primary focus on aerospace and defense work, American Metaseal Corp. of Arbutus, Maryland, has qualified as a Top Shop on multiple occasions.
Read MoreVapor Degreasing Cleaning Fluids for Precision Cleaning
Tergo XCF2 cleaning solution is designed to meet diverse industrial technical cleaning needs with formulas that deliver reliable and repeatable cleaning performance.
Read MoreMicroCare Offers Alternatives to Discontinued Vapor Degreasing Fluids
MicroCare says it is equipped to handle customers affected by 3M's discontinuation of the Novec specialty fluids line with its own products.
Read MoreRead Next
Episode 45: An Interview with Chandler Mancuso, MacDermid Envio Solutions
Chandler Mancuso, technical director with MacDermid Envio discusses updating your wastewater treatment system and implementing materials recycling solutions to increase efficiencies, control costs and reduce environmental impact.
Read MoreDelivering Increased Benefits to Greenhouse Films
Baystar's Borstar technology is helping customers deliver better, more reliable production methods to greenhouse agriculture.
Read MoreA ‘Clean’ Agenda Offers Unique Presentations in Chicago
The 2024 Parts Cleaning Conference, co-located with the International Manufacturing Technology Show, includes presentations by several speakers who are new to the conference and topics that have not been covered in past editions of this event.
Read More