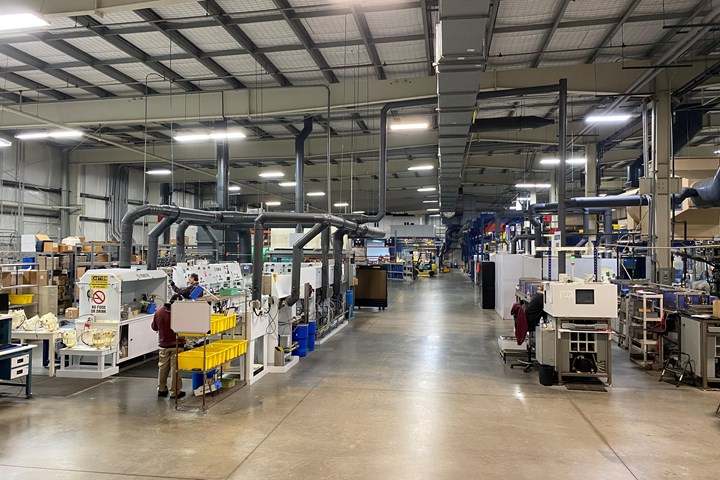
Electro-Spec’s Franklin, Indiana-based facility boasts well-lit workstations, epoxy floors and automated process lines.
Photo Credit: Electro-Spec
The thought of visiting a plating shop in the Midwest that’s been in business since the ‘50s likely conjures the idea of a dark and dank warehouse crammed full of old process tanks and bins of parts. This is exactly the opposite of what you’ll see if you visit Electro-Spec of Franklin, Indiana.
Founded in 1959, Electro-Spec, like many plating operations of that era, got its start as a decorative plating operation. Originally known as Economy Plating, the company has grown into a leading surface finishing company specializing in high-reliability plating for such markets as automotive, aerospace, medical, telecommunication, nuclear, RF/microwave and batteries.
Company president Jeff Smith says the company first got its big break on some NASA projects starting with the Mercury Space Program. From there, Electro-Spec set its sights on high-reliability, function-critical applications requiring a zero-failure rate. Today, the company works with the world’s leading aerospace companies and has been involved with numerous space applications including the Space Shuttle program, Mars rovers and satellites, as well as defense applications. Within the medical sector, Electro-Spec specializes in plating micro-electronic medical components and implantable cardio and neuro-stimulation devices. The company also works with many large telecommunication companies that require precision plating with uniform coverage, exact tolerances and non-magnetic finishes.

Electro-Spec is equipped with sophisticated automated and PLC-controlled plating lines.
Electro-Spec’s 55,000-square-foot Indiana facility is equipped with some of the most sophisticated PLC-controlled plating lines you’ll find anywhere. With integrated statistical process control and software, the company prides itself on precision, reliability and traceability. The company’s range of plating services includes gold, silver, electrolytic and electroless nickel, copper, tin, white bronze and passivation.
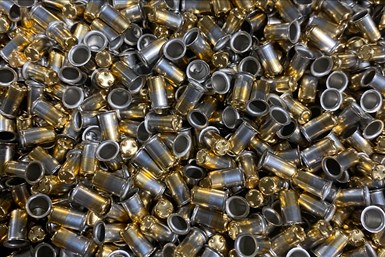
Electro-Spec uses selective plating to apply gold to specific areas of parts.
Dealing with small and complex parts, such as microelectronics and sensors, the company employs numerous specialized plating technologies including selective plating, spouted bed electrode (SBE) plating and its proprietary TRI-M3 (Tri-Alloy, Tri-Metal, or White Bronze) finish. Selective plating using special tooling affords Electro-Spec the ability to apply gold to specific areas of parts with precision. SBE plating technology uses continuous ultrasonic agitation to facilitate part movement, ensuring that each part receives uniform coverage on all surface areas. Electro-Spec’s TRI-M3 plating was developed to provide high corrosion and tarnish resistance for RF and microwave connectors and components.
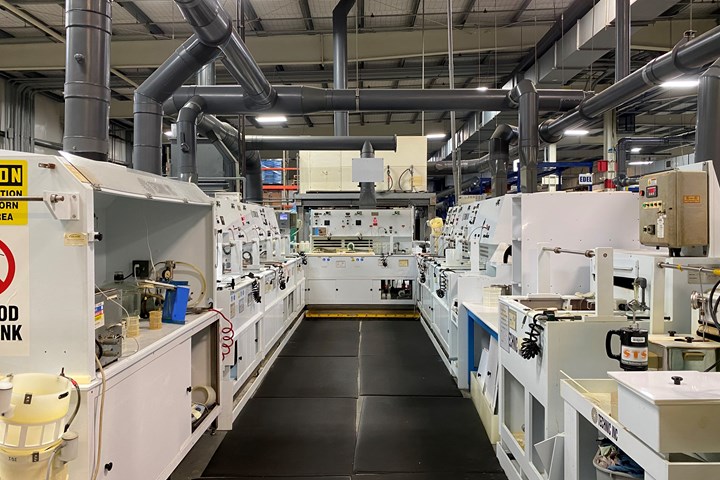
Electro-Spec uses spouted bed electrode (SBE) plating to ensure small parts receive uniform plating coverage.
A Collaborative Approach
For Electro-Spec, reliability of the finish is paramount and the company’s approach to assisting customers involves working with engineers in a collaborative manner to resolve persistent plating problems and exploring novel applications for emerging technologies.
“With our planning and testing capabilities, we’re able to work with our customers, prospective customers and their engineering teams on [developing] new finishes or different ways of plating parts to try to solve problems,” Smith says. “That’s a core part of our business.”
Electro-Spec has implemented a rigorous quality control process employing state-of-the-art technology and equipment. Its testing capabilities include Scanning Electron Microscopy and Energy Dispersive X-ray Spectroscopy, which enable the company to provide failure analysis and to identify the root cause for problems associated with corrosion and wear.
A Perennial Top Shop
Constant improvement is important for any finishing operation, but Electro-Spec seems to truly exemplify that ideal as they’ve evolved as a company. The company is no stranger to Products Finishing’s Top Shops list and has been participating in the Top Shops Program since the very first benchmarking survey was sent out in 2015.
“It was the first opportunity to have some sort of benchmark on quality metrics, personnel, testing capabilities and capital investment,” Smith says. “What I think is great is that from the very beginning — and every single year — there’s more detail. From quoting and pricing to win rates to inventory turns — all these things that have been added in over the years. It’s great to have that data. We look at it and figure out what things we need to do differently.”
Electro-Spec has had its share of growing pains and struggles, including a fire in 2003 that forced them to rebuild. In 2011 the company moved to its current facility. Through it all, the company turned each of these challenges into an opportunity to improve.
Smith says, “As we were moving, we were able to break stuff down and upgrade or refurbish our equipment — and we’ve taken off and grown considerably ever since.”
As the company continued to grow in aerospace, telecommunications and defense it added a Lexington, South Carolina-based facility where it added bright tin and matte tin capabilities. Electro-Spec Carolina has now been operational for four years and has helped the company expand its business in nuclear applications.
Supply Chain Challenges
When asked about business trends that have been the most challenging, Smith points to the disruptions in supply chain that were sparked by COVID and have persisted over the past few years.
“It involves everything from equipment to chemistry to metals — everything that we do,” Smith says. “You’re constantly trying to figure out how to balance it all, making sure you have an adequate supply of chemistry or metals. Then, if you’ve got equipment issues, you have enough critical spare parts to keep things going.”
Smith points out the reactive nature of the finishing industry. “We’re at the tail end of the chain — design, manufacturing, and then plating,” he says. Despite how proactive a finishing operation tries to be, it’s difficult to know what orders will show up and, being at the end of the production chain, there’s often a need to expedite processing. Smith says the constant need to maintain an adequate supply of necessary materials to meet those quick turns is an innate challenge in the industry and that the state of today’s supply chain has greatly exacerbated the problem.
“When you’re a service-based business, you’re already being asked to do the impossible in terms of quick turnarounds,” Smith says. “Having all those contingencies covered in this kind of environment makes it really difficult.”
However, in the end, making it work is what Electro-Spec is all about. So many of the parts the company plates are tiny, some difficult to see with the naked eye — but they are a very big deal. From life-saving medical implants to parts contributing to aerospace, space exploration and defense applications, the finishes that Electro-Spec provides are mission-critical.
Related Content
Advantages to Pumped Eductor Agitation
Not all agitation methods are created equally. Pumped agitation with eductor nozzles can improve process tanks and quickly show a reduction in operating costs while keeping staff safe, following environmental legislation and preventing pollution.
Read More3 Tests to Ensure Parts are Clean Prior to Plating
Making sure that all of the pre-processing fluids are removed prior to plating is not as simple as it seems. Rich Held of Haviland Products outlines three tests that can help verify that your parts are clean.
Read MoreLiquid Chrome Vs. Chromic Acid Flake
Contemplating how to continue offering chromic acid services in an increasingly stringent regulatory world? Liquid chrome products may be the solution you’re looking for.
Read MoreTrivalent Chrome Overview
As the finishing industry begins to move away from the use of hexavalent chromium to trivalent chromium, what factors should finishers consider as they make new investments? Mark Schario, chief technology officer for Columbia Chemical offers a helpful overview of this complicated topic.
Read MoreRead Next
Consistency is Key for this Plating Top Shop
A recurring theme from Products Finishing's recent visit to Varland Plating was a commitment to continuous improvement.
Read MoreCustom Plating Technology Enables Medical Devices
Finisher collaboration during product design delivers plating solutions for medical OEMs.
Read MoreFrom Decorative Beginnings to Advanced Applications
How Advanced Plating Technologies grew from a decorative plating shop to a company specializing in surface engineering for today’s cutting-edge technologies.
Read More