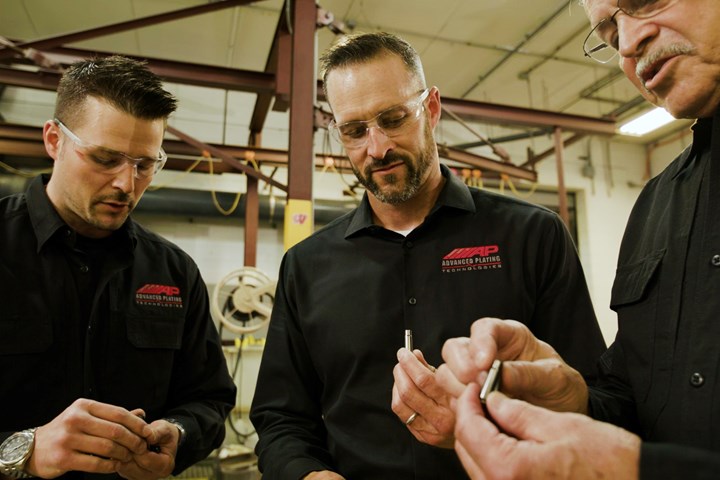
Advanced Plating Technologies is family-owned company rooted in metal finishing that has grown into surface engineering and consulting at a part design level.
Photo Credit: All photos courtesy of Advanced Plating Technologies
Celebrating 75 years in the metal finishing industry, Advanced Plating Technologies (APT, Milwaukee, Wisc.) is a fourth-generation, all veteran, family-owned metal finishing job shop dedicated to providing electrolytic and electroless plating as well as powder coating and passivation services. Today, APT is an industry-leading, ISO 13485:2016 & 9001:2015 certified and ITAR registered job shop that provides engineered solutions in metal finishing within numerous demanding sectors including the electric vehicle, defense, medical, telecommunications, electronic and power distribution sectors, among others. The company provides both new design consulting in surface engineering as well as reverse engineering of existing metal finishing issues including contact cycle life, soldering, brazing or corrosion failures as well as adhesion failures.
APT operates nine production lines in three facilities with a total of 55,000 ft2 and employs 75 persons across multiple production shifts which positions the company in the top 10 percentile of size of job shops across the country.
But, building a company like APT is a story in and of itself. The company’s history is one that illustrates some of the challenges those working in the finishing industry have faced over the years and how finding a niche is one of the keys to finding success.
Decorative beginnings
Advanced Plating Technologies was originally founded in 1948 as Artistic Plating Company by James H. Lindstedt, Harry C. Lindstedt and Earl Herrington. The company began as a simple job shop that serviced retail accounts and a mix of small- to medium-volume production orders.
“We were a very different company for most of my life growing up,” says APT president, Matt Lindstedt. “Like a lot of metal finishing companies, it started small, plating anything they get their hands on — a lot of it was retail work. The name of the company, Artistic Plating, was an apt name, because the company did a lot of decorative work.”
Artistic Plating Company grew steadily through the years, developing a commercial/production focus within the regional plumbing, power distribution and industrial markets.
“The company really grew out of decorative finishing, even though we always serviced the power distribution market — our industrial base was tin, silver and nickel in those markets. It was about 80% decorative and 20% industrial. The company really did well with decorative finishing through the late 80s and the 90s, and developed a number of proprietary finishes for the plumbing industry,” Lindstedt says.

APT’s background in power distribution has translated into expertise in trends in such markets as electronics, medical and electric vehicles.
Shifting focus
As the company grew in finishing capabilities and engineering expertise, the strategic focus shifted into more technical markets where multi-generational experience in metal finishing could be leveraged to provide metal finishing solutions. The shift wasn’t an immediate one and was sparked by some challenging times for the company. A series of unfortunate events including a downturn in its plumbing business due to offshoring, a fire that burned the company’s main plating building to the ground in 1996 and the Great Recession of the late 2000s gave Artistic Plating Company an opportunity to rethink its business strategy.
“People always look at me kind of funny when I say that the best thing that ever happened to the company hands down was the Great Recession,” Lindstedt says. “But, we got so slow that it was a moment in time where we could really think about not what we are, but we wanted to become.”
The evolving company began to see opportunity in the fact that finishing is specialized, and oftentimes even very large and sophisticated OEMs lack a core understanding of metal finishing principles.
“I realized we were dealing daily with people in big companies that didn’t really understand surface finishing,” Lindstedt says.
The company made its new mission to fill this void and become a surface engineering resource for its customer base. In 2013 the name of the company was changed to Advanced Plating Technologies to reflect its new strategic focus.
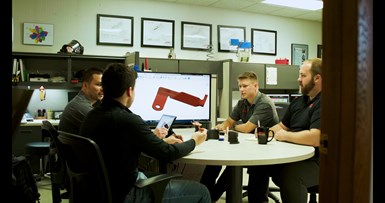
APT’s focus is on surface engineering for some of the most advanced technologies requiring finishes today.
Right place, right time
APT’s efforts to reinvent itself placed the company right in step with trends in the manufacturing world today. The company’s background in power distribution and precious metal deposition translated into expertise in trends toward the electrification of … well, everything. Lindstedt says the mission is to serve industries that are exploring cutting-edge technologies in a variety of industries.
“If there’s one thing we’ve always done really well in this company — we’re really good at getting electricity from point A to point B,” he says. “Whether that’s moving the electrons within a vehicle, minimizing heat within connections, improving relay performance, or whether it's in switchgear and/or transformers that provide the charging power for all types of devices, we see a need for gold plating, and silver plating in so many areas because everything today is monitored, controlled and connected. And that’s only going to continue.”
APT’s experience with power distribution has made the company a leader in such markets as telecommunications, electronics, medical, and, of course, electric vehicles. Prior to the ramp-up in EV production, APT didn’t have a great deal of business in the automotive market.
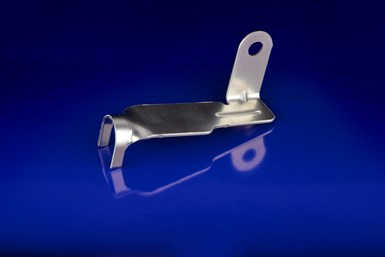
EVs continue to increase the need for conductive finishes in the automotive market.
Lindstedt explains, “So as a company, historically, we were largely into conductive finishes: silver, gold, tin, lead, nickel, copper. For the most part, the automotive industry did not use a ton of those finishes, and if they did use silver or tin, it tended to be much more for reel-to-reel plating. We’ve always been a loose piece plater.”
“Honestly, internal combustion engines don’t need a lot of metal finishing as a whole,” he adds. “There’s limited finishing within an internal combustion engine, but nothing like an EV. An EV is a power station on four wheels.”
Today, APT looks to the EV market as an area of increasing opportunity for exactly the kind of work where the company thrives — design and engineering. With the automotive industry actively working to find the best ways to make EVs, the time is ripe for collaboration and innovation — and in the finishing realm that translates to surface engineering. The explosion of the electric vehicle market has presented additional surface finishing opportunities within the battery and power storage markets.
“It’s a developing industry,” Lindstedt says. “Whenever there’s a developing industry, the need for collaborative work is much higher.”
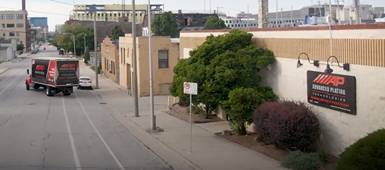
APT operates nine production lines in three facilities with a total of 55,000 ft2.
Passion for the industry
APT’s history reflects many of the struggles that the finishing industry itself has endured. From trying to stay afloat during economic downturns to seeing work in many of its traditional markets siphoned away as industries sought to cut costs by manufacturing in China. But the company’s passion for surface engineering has kept them moving forward and constantly seeking relevant and interesting work.
Today, Lindstedt is excited about what lies ahead for the finishing industry. The past few years have been a challenge for everyone, but perhaps because they’ve weathered storms before, he prefers to look at the opportunities that lie ahead. He says that in the wake of COVID and everything that came with it from material shortages to shipping disruptions to price increases, the manufacturing landscape looks much different than it did just a few years ago.
“It made people realize that you have to have robust supply chains,” Lindstedt says. Logistic chains that must cross thousands of miles of ocean have demonstrated their vulnerability especially if nations become political adversaries.
Reinvestment in American manufacturing comes at a time when the world is looking for solutions to so many challenges such as keeping up with the rapid evolution of global communications to sustainability to environmental concerns to infrastructure requirements and the evolution of transportation.
“It’s an exciting time,” Lindstedt says. “You’re not even going to recognize the world twenty years from now from where it is today — and that’s way beyond just EVs. So many industries are investing in interconnectivity, technology and autonomous controls. I think it’s a kind of the second industrial revolution in this country.”
Related Content
Products Finishing Reveals 2024 Qualifying Top Shops
PF reveals the qualifying shops in its annual Top Shops Benchmarking Survey — a program designed to offer shops insights into their overall performance in the industry.
Read MoreInnovation in Plating on Plastic
Plating on advanced plastics solution offers improved adhesion, temperature resistance and cost savings.
Read MoreTrivalent Chrome Overview
As the finishing industry begins to move away from the use of hexavalent chromium to trivalent chromium, what factors should finishers consider as they make new investments? Mark Schario, chief technology officer for Columbia Chemical offers a helpful overview of this complicated topic.
Read MoreNanotechnology Start-up Develops Gold Plating Replacement
Ag-Nano System LLC introduces a new method of electroplating based on golden silver nanoparticles aimed at replacing gold plating used in electrical circuits.
Read MoreRead Next
A ‘Clean’ Agenda Offers Unique Presentations in Chicago
The 2024 Parts Cleaning Conference, co-located with the International Manufacturing Technology Show, includes presentations by several speakers who are new to the conference and topics that have not been covered in past editions of this event.
Read MoreEducation Bringing Cleaning to Machining
Debuting new speakers and cleaning technology content during this half-day workshop co-located with IMTS 2024.
Read MoreDelivering Increased Benefits to Greenhouse Films
Baystar's Borstar technology is helping customers deliver better, more reliable production methods to greenhouse agriculture.
Read More