Forms+Surfaces Expands from Humble Beginnings to Global Market Leader
Originally founded in Santa Barbara, California, the company now manufactures in multiple U.S. locations and in India.
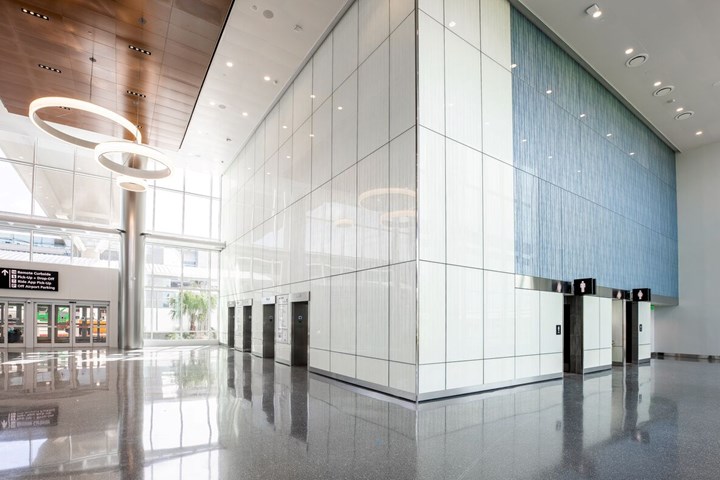
From decorative wall panels to elevator doors and ceiling panels, Forms+Surfaces offers high-end finished products to designers and builders around the world.
Photo Credit: Forms+Surfaces
High-end indoor architectural products, as well as outdoor products for commercial and municipal installations, require finesse and endurance in their finishes, as they need to stand up to the rigors of constant human interaction, as well as environmental stressors of weather. Forms+Surfaces has built an incredible business, spanning the globe, as a full-service design and manufacturing company for outdoor products that include: park benches; trash receptacles; light poles; parking and pathway bollards; planters, and much more for outdoor installation. These products are fabricated and finished outside of Pittsburgh, Pennsylvania, at the company’s global headquarters. In Phoenix, Arizona, and Pune, India, indoor architectural elements such as doors and door pulls, elevator panels, and wall cladding, are produced. And across the world, a sales force sells all these products to a variety of architects and designers for projects that require not just functional, but beautifully formed furniture and finishes.
Founded in Santa Barbara nearly 50 years ago, Forms+Surfaces has continued to grow its footprint and expand its capabilities. A few members of the Products Finishing team were fortunate to visit the Pittsburgh facility earlier this year during the Chemical Coaters Association International (CCAI) Women In Finishing (WIF) conference held nearby. To say the facility was impressive would be an understatement.
Full-service fab and finishing
The fabrication side of the Pittsburgh shop includes a fiber laser, punch press, brake press and small machine shop, as well as robotic welding stations. With about 120 production employees in the facility, they also run a fully integrated wood shop where they cut and process lumber from raw materials— particularly environmentally friendly Brazilian hardwoods — into slats for benches and receptacles.
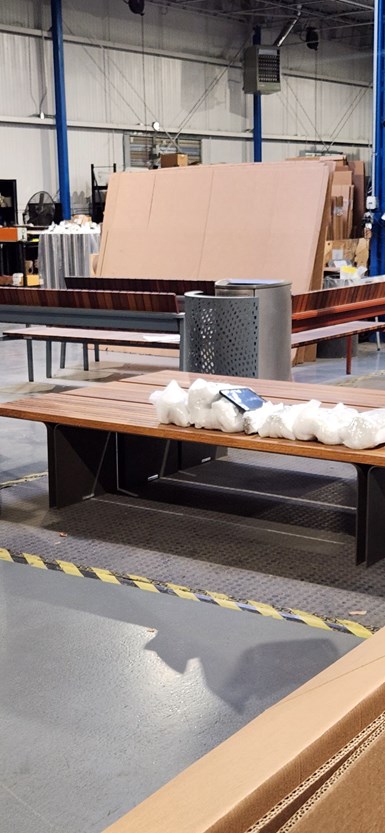
Benches and receptacles in final assembly, constructed of wood and metal panels fabricated by F+S.
Photo Credit: Products Finishing
Forms+Surfaces’ Pittsburgh operation started as a much smaller organization, but as the business grew, they were able to justify the purchase of more equipment and grow their shop footprint. Just over two years ago, the shop made a significant capital investment in an automated powder coating line, a major upgrade from its previous 12-ft by 12-ft electrostatic booth and oven. Prior to this purchase, the shop moved from two smaller buildings to a brand-new facility that would accommodate all of its operations under one roof.
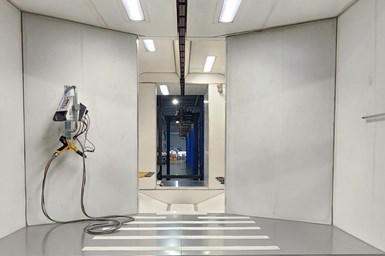
Looking into the automated powder coating line oven at the Pittsburgh location.
Photo Credit: Products Finishing
The automated powder coating line has changed their business substantially. “Before the robotic line, powder coating was a very manual process for us,” the company says. “We used to meet almost every day to discuss how to powder coat various parts the most efficiently and effectively.” Today, the line can run continuously if there is work. The line doesn’t have a prewash setup, so an outside company does chromate dip pretreatment when needed.With 16 standard colors, color changeouts are now extremely easy, taking from 15-17 minutes to changeover colors, with 6-7 color changes per shift. The company can accommodate custom colors and use manual spray guns for challenging projects or unique shapes or small runs. They also recycle all the powder overspray, saving up to 30% of what used to be wasted with their manual processing. The quality department inspects all final parts and cleans them up as needed, ensuring that customers are receiving the very best products.
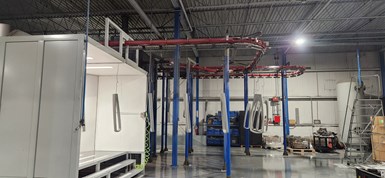
Suspended parts after finishing final curing in automated powder coating line. Photo Credit: Products Finishing
Known for its innovation, quality, ability to deliver and exceptional in-house capabilities, F+S can perform a wide array of manufacturing and finishing to create just about anything. Standard product delivery is eight weeks, but because several of their landscape architecture and municipal customers often order products well in advance of when it’s needed, they have a large storage facility where all inventory is RFID tagged and stored until needed. And with its excellent reputation, Forms+Surfaces is the global supplier of signage and wall cladding for the retail outlets of one of the world’s most famous consumer product brands. They supply icons and logos that have been fabricated from sheet metal, painted and finished to be shipped out to retail outlets around the world.
At the Phoenix operation, Forms+Surfaces focuses on interior products. This location primarily works with metals, glass and veneers, and doesn’t have a wood fabrication shop like Pittsburgh does. There is also a “twin” facility in Pune, India, with the same capabilities as the Phoenix plant, that manufactures and supplies products across Asia and Europe to keep shipping costs more controlled and prices lower for customers.
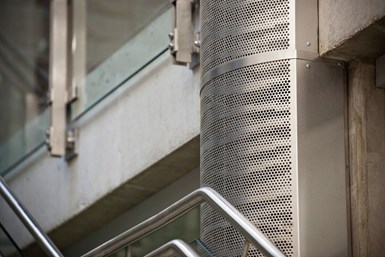
F+S offers both metal and glass finished materials for interior functional and purely design elements.
Photo Credit: Forms+Surfaces
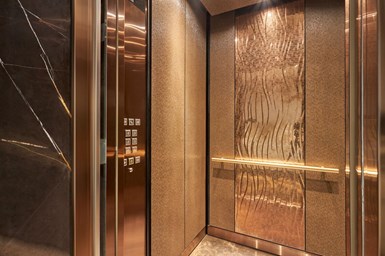
Texturized and coated elevator wall panels.
Photo Credit: Forms+Surfaces
In addition to welding booths, brake presses and other equipment the Pittsburgh shop has, Phoenix also has wide format printers, water jet cutters and glass kilns, as well as specialty glass processing equipment, to create cast and patterned glass panels for interior spaces. The Phoenix plant’s operations manager says while the shop works with standard colors and patterns, they also produce a lot of custom materials, and can even match their glass products to standard paint colors and finishes. While they don’t do powder coating in Phoenix, they do other finishing and coating operations, and developed a proprietary product called Ceramiloc+, a final finishing treatment offering an invisible protective coating that increases fingerprint resistance and makes maintenance easier on stainless steel products. Because so many of their final products are in high-touch environments like elevator walls, this finish allows customers to maintain mark-free walls without showing every fingerprint or accidental touchpoint that would typically leave a smear or mark on the walls.
Atypical staffing needs
Because most of the products manufactured by Forms+Surfaces are their own designs, the company employs a variety of staff with architectural, design and engineering experience, including some sales staff that are accredited by the American Institute of Architects (AIA) and RID (Residential Interior Design). But Forms+Surfaces doesn’t hire employees just based on what they see on their resumes — having the right attitude and motivation are just a few things they look for.
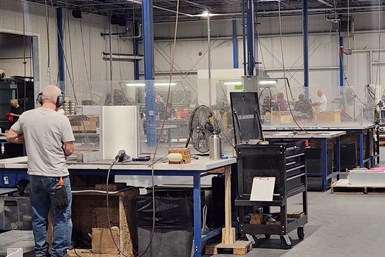
View of a few of the finishing assembly stations at the Pittsburgh facility.
Photo Credit: Products Finishing
Process engineers are also seen walking the shop floor, observing different work areas as they try to create new processes and procedures for more efficient workflows. The robotic welding stations are a key focus for them in Pittsburgh, trying to create programs that eliminate steps and additional operations through automation. The leadership team allows its diverse staff to all contribute ideas for better production, workflow and even new products.
With some of the top interior designers for commercial projects as their key customers, Forms+Surfaces plans to remain a market leader. The company states on the following in its promotions: “No matter what the size or scope of a job, we embrace our role as an innovative, responsive partner that architects and designers can rely on and trust.” With a focus on unique, high-end products, the company is poised for continued global growth in all its operations.
Related Content
12 Ways to Improve Your Powder Coating Quality
Often overlooked powder coating procedures that can help you elevate your quality, streamline your operations and improve your profitability.
Read MoreSelecting the Right Outdoor-Durable Powder Coating
The powder coating industry offers an array of chemistries to provide an excellent match to the manufacturer’s expectations for outdoor durability.
Read MoreHow to Address Declining Powder Coating Coverage Over Time
Fine particles from reclaim could be to blame for powder coating problems that emerge over time. Avoid problems by keeping hooks clean, maintaining guns and using reclaim powder quickly to avoid accumulation of fines.
Read MoreLow-Temperature-Cure Powder Coatings Offer Unique Opportunities
An in-depth look at the advantages of low-temperature-cure powder coatings and the considerations for incorporating them into your process.
Read MoreRead Next
Delivering Increased Benefits to Greenhouse Films
Baystar's Borstar technology is helping customers deliver better, more reliable production methods to greenhouse agriculture.
Read MoreEducation Bringing Cleaning to Machining
Debuting new speakers and cleaning technology content during this half-day workshop co-located with IMTS 2024.
Read MoreA ‘Clean’ Agenda Offers Unique Presentations in Chicago
The 2024 Parts Cleaning Conference, co-located with the International Manufacturing Technology Show, includes presentations by several speakers who are new to the conference and topics that have not been covered in past editions of this event.
Read More