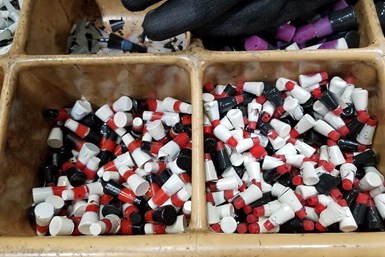
Q. We are having issues with plug loss and leakage during coating. Rework is expensive – how can we mitigate this?
A. Excellent question! There are many factors that influence plug loss or leakage. Here are some recommendations for avoiding plug loss, leakage and rework.
Use the correct plug size
Incorrect plug size selection issues are surprisingly common, especially when manufacturers only convey hole or thread sizes to the purchasing department.
In immersion or heat cycles, building pressure can trap large air pockets. If you do not select plugs with this problem in mind, a “perfect fit” on paper may be the wrong choice, and a slightly oversized option may prove better.
Alternatively, if a tapered plug is too large, it may not seat far enough into the hole to be secure. As the parts move down the line, unsecured plugs may fall out. When properly inserted, a correctly sized tapered plug should have half of the total length of the plug exposed.
Use the correct plug type
While basic tapered plugs are popular due to their flexibility in what size holes/threads they can mask and their low relative cost, other plug variations can better suit your specific needs. For example, using a tapered plug with a handle can simplify proper seating, and flangeless plugs incorporate a handle and ribs that fit well into threaded holes to create a tighter seal.
Tapered plugs have trouble resisting the influences of pressure and may pop out, especially when used in threaded holes with little surface contact between the plug and part. In these cases, a threaded plug with a hex head is more stable, with the hex head allowing you to insert an electric driver for increased efficiency and ergonomics.
Bore mask plug combinations are excellent for enclosed large shafts and tubes. This type of masking solution uses a tapered plug with a hole in the center. After inserting a “noodle” with an integrated washer through the hole, you can pull the tail tight to snug the plug into place, repeating the process with another plug on the opposite end. The elasticity of the rubber noodle will produce enough opposing force to prevent the plugs from popping out when internal pressures increase with heat.
Pay attention to the plug’s lifespan
You should always test the expected lifespan of masking in your particular process. Silicone has the best heat resistance for masking, but also has a limitation to the number of duty cycles it can endure. Repeated heating and cooling will cause silicone plugs to dry and become less pliable. Infrared (IR) ovens exacerbate the issue: while the temperature at the top of the oven may be well under silicone’s limit, source temperatures are often two or three times the material’s maximum temperature rating. Although silicone does not melt, it will become brittle, which decreases the plug’s functionality. Harsh chemicals used in plating can also accelerate this degeneration.
Use custom solutions
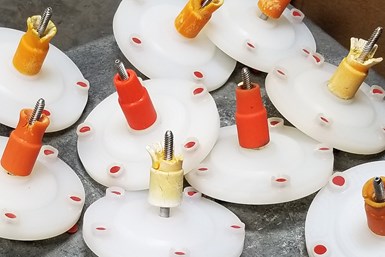
Sometimes paying for a custom solution is unavoidable — standard plugs won’t always perform as needed, and the cost of rework can outpace the cost of a custom mask. Custom vent plugs allow air to escape without letting liquids enter. This can be critical in wash cycles and submersion processes like e-coating and plating. In other situations, a custom size could be your best solution. Use the expertise of your masking provider to devise parts that will solve your unique problem.
The best course of action when plugs fail is to contact your masking supplier. Usually, they have dealt with a similar situation and can provide immediate alternatives, keeping you on track!
Related Content
How to Maximize Nickel Plating Performance
The advantages of boric acid-free nickel plating include allowing manufacturers who utilize nickel plating to keep up the ever-changing regulatory policies and support sustainability efforts.
Read MoreHow to Choose Between Sulfate and Chloride-Based Trivalent Chromium
There are several factors to consider when choosing between sulfate and chloride-based baths for trivalent chromium plating. Mark Schario of Columbia Chemical discusses the differences and what platers should keep in mind when evaluating options.
Read MorePrevent Plating Problems with Critical Inspections
Tanks and their contents should be regularly inspected visually and analytically. When a quality issue arises, it is important to quickly pinpoint where the main problem is by checking which parameter is out of line.
Read MoreRead Next
How to Mask Common Part Features for Liquid and Powder Coating
Q. Could give us some tips on making sure we are using the proper masking tools for our parts. Masking expert Andrew Oniszczuk from EPSi answers this reader’s question.
Read MoreCFS Expands Electropolishing Services to Additional Markets
After providing electropolishing services to the industrial manufacturing industry for more than 20 years, Custom Fab Solutions has announced it is expanding its offerings to additional markets including food and beverage, medical devices and aerospace.
Read MoreCFS' Masking Plugs Are Color-Coded for Accuracy of Selection
The plugs are especially suited to e-coating and other immersion processes.
Read More