Mechanical Finishing to Enhance Plating Operations
Combination swing-frame grinder cuts production time at Lincoln Industries.
Lincoln Industries continues to optimize its vertical integration of tube bending, polishing and plating in order to better serve its customers.
A family-owned business founded more than 60 years ago, the company has more than 600 employees in Lincoln, Nebraska, and provides a comprehensive range of manufacturing and engineering services for products that require high-performance metal finishing.
Among Lincoln’s primary products are chrome-plated exhaust stacks for major heavy-duty truck manufacturers and the aftermarket truck industry under the Lincoln Chrome brand. To make the exhaust stacks, the company starts with welded steel or stainless steel tubing in sizes ranging from 5-inch to 8-inch OD, and lengths from 24 to 120 inches. These are formed and bent to the configurations seen on heavy-duty trucks across the country. Before they can be plated, the longitudinal welds and any surface imperfections must be polished.
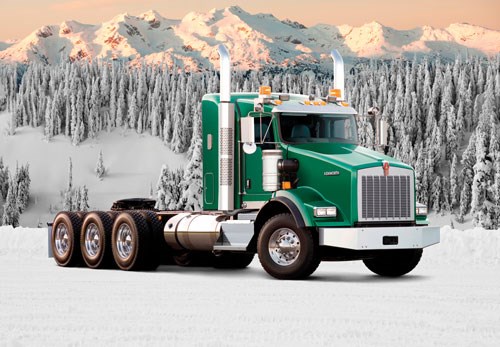
Kentworth trucks sport the shiny stacks.
“The plated finish is directly proportional to the condition of the base metal,” says Eric Rempel, a Lincoln controls engineer. “A scratch or ding will show right through it.”
To improve its polishing operation, Lincoln consulted with Grinding & Polishing Machinery Corp. of Indianapolis, a specialist in designing and building industrial grinding and polishing machinery. G&P, which had supplied polishing equipment to the company previously, worked with Rempel and Process Specialist Jason Eickhoff at Lincoln to design and build a new machine component that would make their polishing process more efficient and reduce production cycle times.
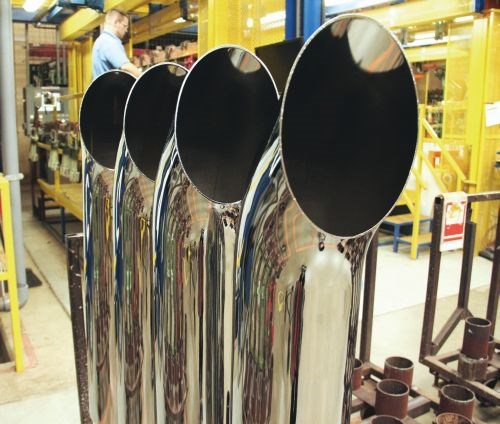
Chrome-plated exhaust stacks and truck accessories are a major Lincoln Industries product. Above:Stacks are polished and chromed at their Nebraska plant.
The machine uses a single driving mechanism to drive two heads: a belt grinder and a buffing wheel. The simple but effective concept uses the grinding belt to drive the buffing wheel, which is mounted at the opposite end of the same shaft as the belt’s contact wheel. The entire grinding mechanism is built on a swing frame that allows the operator to control the positioning and pressure of whichever grinding head is being used. It also lets the operator pivot the unit to change a belt when necessary. The machine’s control bar is adjustable to accommodate operators of different heights for better ergonomics.
Framework Design
To complete the machine, Lincoln Industries had a framework designed and built locally to suspend the grinding unit and position the part being polished.
Rempel designed controls that enable the operator to select from a range of parameters, including tube diameter, bed and belt speeds and many other variables. When changing from one head to another, the operator simply selects a setting for either belt or flap wheel on the control panel. A pneumatic cylinder then positions the appropriate G&P head over the workpiece and the controls set the variable speed drive motor to the proper speed.
Once a part is mounted in position, the belt is started and the travel cycle begins. At the end of the travel, the operator indexes the part and repeats the process, continuing around the part diameter in this manner. He then selects the flap wheel setting and the machine resets to the proper position and speed, after which the polishing process is repeated using the wheel.
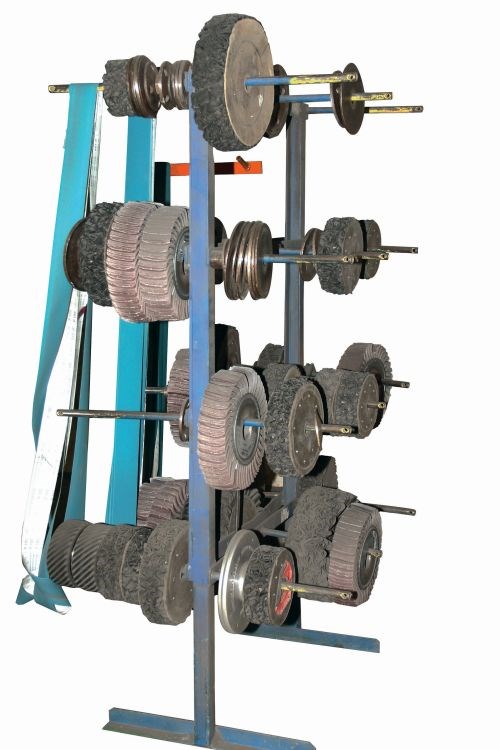
Above, a combination buffer/abrasive belt grinder reduced the time to polish truck exhaust stacks before plating by more than 40 percent at Lincoln Industries.
Operator skill is an important part of the process, because the polished steel or stainless steel must be as flawless as possible before plating. Rempel says that the machine’s programmed capabilities are enhanced with skilled hand-eye coordination by the operator to achieve superior results. For example, if the operator sees a flaw in the part, he can make multiple passes with the abrasive belt or wheel instead of indexing the part for the next pass. This ensures all parts meet Lincoln Industries’ and the OEM’s high standards of finish.
“Now we can run the same part through both operations with one setup, which reduces the possibility of handling damage,” Rempel says. “Having fewer handling operations also helps prevent repetitive motion injuries for the operator.”
For information on Lincoln Industries, visit lincolnindustries.com; for information on Grinding & Polishing Machinery Corp., visit gandpmachineryin.com.
Originally published in the December 2015 issue.
Related Content
3 Tests to Ensure Parts are Clean Prior to Plating
Making sure that all of the pre-processing fluids are removed prior to plating is not as simple as it seems. Rich Held of Haviland Products outlines three tests that can help verify that your parts are clean.
Read MoreHow to Choose Between Sulfate and Chloride-Based Trivalent Chromium
There are several factors to consider when choosing between sulfate and chloride-based baths for trivalent chromium plating. Mark Schario of Columbia Chemical discusses the differences and what platers should keep in mind when evaluating options.
Read MoreLiquid Chrome Vs. Chromic Acid Flake
Contemplating how to continue offering chromic acid services in an increasingly stringent regulatory world? Liquid chrome products may be the solution you’re looking for.
Read MoreHow to Maximize Nickel Plating Performance
The advantages of boric acid-free nickel plating include allowing manufacturers who utilize nickel plating to keep up the ever-changing regulatory policies and support sustainability efforts.
Read MoreRead Next
Raising the Bar on Polishing
Glastender builds bar equipment faster thanks to AM Machinery, Autopulit.
Read MoreEducation Bringing Cleaning to Machining
Debuting new speakers and cleaning technology content during this half-day workshop co-located with IMTS 2024.
Read MoreA ‘Clean’ Agenda Offers Unique Presentations in Chicago
The 2024 Parts Cleaning Conference, co-located with the International Manufacturing Technology Show, includes presentations by several speakers who are new to the conference and topics that have not been covered in past editions of this event.
Read More