Coating Systems with the Best Long-Term Performance
The best protection against corrosion and UV exposure, says Axalta’s Mike Withers, is electrocoat and a super durable powder coating.
Q: What coating system gives the best long-term coating performance?
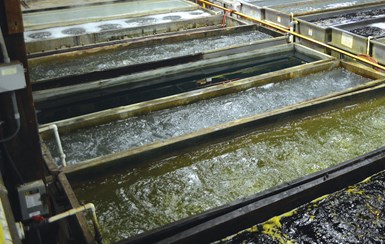
A: If I were asked what gives the best protection against corrosion and UV exposure, it would be electrocoat and a super durable powder coating. Whether you have a zirconium pretreatment system or zinc phosphate pretreatment system, either will give very good corrosion performance. The super durable powder coating will give the best weathering performance, meaning color fade and gloss retention in sun-exposed areas.
There are other options, such as a two-layer powder coating system where the primer layer is an epoxy or an epoxy-polyester hybrid. The primer could also include a sacrificial element such as zinc. It requires a significant loading of zinc to get the long-term performance and that significantly increases the specific gravity, which reduces the square footage per pound of powder coating. It also increases the cost per pound. It’s a pretty big economic impact as it requires more powder and costs more. Newer epoxy primers can give very good performance without the zinc additive.
Looking at the electrocoat and powder coating scenario, you will have the higher cost of two coating lines, but there are many advantages that come with the electrocoat scenario. Let’s look at what they are:
- Film Build Control
- Uniform Film Thickness
- High Throwpower
- Corrosion Protection
- Edge Coverage
- High Throughput
Let’s begin with ‘what is electrocoat?’ It is a synthetic polymer held in a water suspension then, through an electrical current, it is deposited onto a part and then cured in an oven. The electrical current is supplied by a rectifier and can be dialed in to precisely control the film build on the part. The rectifier sends the current to the bath through the anodes, which are typically on the side walls of the tank that holds the electrocoat, and will naturally apply the coating to the closest parts first. Electrocoat can insulate the part during the application process and, thereby, stop the coating process. Electrocoat is typically applied at 1.0 mils or less. The latest generation of electrocoat can give superior corrosion protection at film builds lower than were previously were able.
The term throwpower refers to the electrocoat being deposited on the exterior part and penetrating to the inside parts of the load bar. There is generally a difference between the film build on the exterior parts and the interior parts on the load bar. The latest technology electrocoat will minimize that difference and, thereby, reduce the applied cost. Throwpower can also get complete coverage of geometrically complex parts.
Why is that important? With powder coating, very complex parts can be difficult to get complete coverage. With the electrostatics of the powder coating application, a phenomenon called Faraday cage can occur. This is where it is difficult to get powder coating into tight recesses on parts. There are many application tricks and formulation tricks to improve the ability to get powder in there, but sometimes, regardless of everything you try, you just can’t get powder in there.
With electrocoat, throwpower will get coverage everywhere. The exception would be inside small diameter tubes, but even then you get some coverage inside the ends of the tube. This would mean that, at least from the corrosion protection aspect, you have coverage with electrocoat.
Corrosion protection is usually defined by an accelerated corrosion test. Neutral salt spray has been around for many years, but doesn’t translate to number of years of field performance. Still, it is often used as the test for corrosion performance. You might have heard, “I need 1,000 hours of salt spray.” That is only part of the picture. You also need to define the allowable creepage. The creepage is the amount of undercut of the coating during the testing process. The test begins with a scribe down to bare metal. The part or panel is then placed into a cabinet where warm water with a 5% salt solution is constantly misted on the part/panel. You will get corrosion in the scribe area, but it will also try to migrate under the coating. Once the hours of testing are complete, the loosely attached coating is removed, often with a plastic scraper and the creepage is measured.
Edge coverage is exactly what it sounds like. With many manufacturing processes today, you get a very sharp edge on the part and the coating just doesn’t want to cover those edges well. Today’s best electrocoats have been engineered to give superior edge coverage.
Epoxy electrocoat only cannot be placed in UV-exposed environments. The super durable powder coating gives the weathering protection that you need. It also gives the flexibility of unlimited color options.
What is important in deciding what super durable powder coating to use? The term super durable has been used for quite some time, but it doesn’t give a specific coating performance. The term refers to extended weathering performance. Most coaters I have spoken with think this refers to the resin, which is partly true. You need the pigments and extenders to give the same extended weathering performance as well or you will only get gloss retention with the super durable resin.
When you are looking at super durable powder coatings, it’s a good idea to inquire about the South Florida weathering performance of that coating. The coatings industry tests their coating on panels that are on racks in South Florida. It has one of the harshest exposure areas in the U.S. Remember, you want to check the gloss retention and color fade performance. Almost all coatings will lose gloss and color over time when exposed to the sun. A performance specification defines how much loss is acceptable.
It is important to explain that not every color is available to give five years of South Florida weathering performance. High chroma colors (such as bright orange, red, yellow and others) are not capable of holding their color retention in that harsh UV exposure. Check with your coating supplier to see what is and is not available.
What does this all cost? Electrocoat typically has a higher capital cost, but a lower operating cost than powder coatings. Super durable powder coatings do cost more than standard durable, but their gloss retention and color fade performance is significantly better than standard durable.
If you are considering putting in new equipment, it is recommended to meet with a pretreatment supplier, coating supplier and the systems house from the beginning. The coatings can be engineered to meet your requirements.
Michael Withers is segment leader for architecture and electrocoat (powder group) for Axalta Coating Systems. Visit Axalta.com
Related Content
How to Choose Between Sulfate and Chloride-Based Trivalent Chromium
There are several factors to consider when choosing between sulfate and chloride-based baths for trivalent chromium plating. Mark Schario of Columbia Chemical discusses the differences and what platers should keep in mind when evaluating options.
Read MoreTop Reasons to Switch to a Better Cleaning Fluid
Venesia Hurtubise from MicroCare says switching to the new modern cleaning fluids will have a positive impact on your cleaning process.
Read MoreAnodizing for Bonding Applications in Aerospace
Anodizing for pre-prep bonding bridges the gap between metallic and composite worlds, as it provides a superior surface in many applications on aluminum components for bonding to these composites.
Read MoreConveyors and Paint Systems
Choosing the right conveyor system, coating technology, and ancillary equipment.
Read MoreRead Next
Education Bringing Cleaning to Machining
Debuting new speakers and cleaning technology content during this half-day workshop co-located with IMTS 2024.
Read MoreEpisode 45: An Interview with Chandler Mancuso, MacDermid Envio Solutions
Chandler Mancuso, technical director with MacDermid Envio discusses updating your wastewater treatment system and implementing materials recycling solutions to increase efficiencies, control costs and reduce environmental impact.
Read MoreA ‘Clean’ Agenda Offers Unique Presentations in Chicago
The 2024 Parts Cleaning Conference, co-located with the International Manufacturing Technology Show, includes presentations by several speakers who are new to the conference and topics that have not been covered in past editions of this event.
Read More