Preventing Corrosion in Small Areas
Powder coating expert Rodger Talbert discusses how to get proper cleaning and coverage in tight Faraday areas.
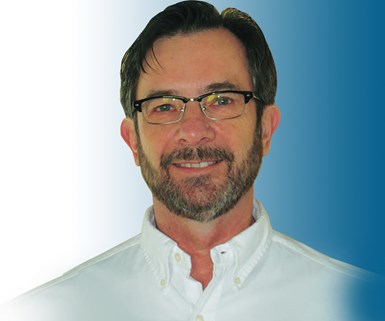
Rodger Talbert has more than 30 years of experience in the powder coating industry.
Q: We took on a job about one year ago, powder coating a new version of the traditional outdoor patio glider; the bench-style outdoor rocking chair. We are doing a sandblast, zinc prime and topcoat with a TGIC polyester powder. Our customer has had some complaints about rust in the area where the expanded metal seat fits into the formed frame. What do you suggest we change or add to our process to fix this problem? What is causing this failure in that particular area of the part? The coverage looks good when the part is done and we do not know what to do next.
A: The rust you describe is located in an area that would be hard to get completely clean and challenging to get complete coverage with that tight Faraday area. It is inside a formed slot formed by the metal fabrication where the steel of the seat fits into the frame. If any corrosive foreign material is left inside the affected area before it is coated, it can set up a corrosion site and begin to corrode as moisture penetrates into the slot and sets off oxidation. It would not take much dirt, old paint, rust or other foreign material to start a corrosion cell in a tight area like that. If a corrosion cell was present before you coated, your good work was wasted. In addition, your coverage in that area may be a little thin or have some very small voids that can set up corrosion.
A thorough blast might get all of the shop dirt and other soils out of the slot, but I think you may need an acid solution or something to be sure you get it down to bare metal and get rid of any contamination.
If it is possible for you to acid pickle the bench, I would consider this a better way to soak out any traces of dirt and scale in that small area. If you cannot immerse them, get an acid solution and apply it using a brush. Let it soak long enough to break down any remaining soil and then pressure rinse it with DI or RO water, dry it and proceed with the primer.
It would also be helpful to consider a second coat of the polyester powder to help fill the space and cover it sufficiently to avoid premature corrosion. Be sure to test for good inner-coat adhesion and avoid applying too thick (to the point that the powder runs). Put a little more work into the area where the problem occurs and that should take care of it and provide the long-term corrosion resistance needed.
Related Content
-
Understanding and Managing White Spots on Anodized Aluminum
Having trouble with spotting defects when anodizing? Taj Patel of Techevon LLC offers a helpful overview of the various causes of white spots and potential solutions.
-
10 Anodizing Best Practices
Following this list of guidelines can help to increase the performance, cost effectiveness and quality for your anodizing operation.
-
Masking Solutions for Medical Applications
According to Custom Fabricating and Supplies, a cleanroom is ideal for converting, die cutting, laminating, slitting, packaging and assembly of medical-grade products.