Reducing Downtime Due to Clogging
Jacob Fortmeyer of Carlisle Fluid Technologies discusses ways to avoid clogging and seizing of liquid coating systems.
Jacob Fortmeyer of Carlisle Fluid Technologies discusses trends in automation and smart technologies for finishers.
Q: We have a plural-component proportioner that clogs frequently and causes unplanned maintenance of the flowmeters, valves, and other fluid components, requiring production stoppages. How do we reduce this downtime?
Clogging, seizing, and flowmeter pack-out are some of the most common causes of unexpected downtime for plural-component equipment. This downtime hurts productivity and can shut down an entire process while the cause of the issue is investigated. In addition, equipment that is seeing this kind of build-up is also much more likely to be operating off-ratio and unable to deliver consistent flow, reducing your finish quality even while the system is operational. This can lead to increased rework and product quality issues if not caught quickly.
But the occurrence of these issues can be significantly reduced or eliminated through the implementation of certain process controls and plural-component best practices. These include proper fluid filtration, eliminating moisture in the lines, never mixing incompatible coatings in the same equipment, and proper flushing. These four guidelines apply to almost any plural-component equipment, from entry-level manual proportioners to advanced automatic systems.
Coating Filtration
The number one cause of plural-component equipment clogging and pack-out in the field is missing or inadequate fluid filtration. Coatings of many different types will tend to form larger particulates, sediment and crystals over time in both static pressure pots and drums, as well as in circulation systems. If not properly filtered, these objects will enter your equipment and embed themselves in difficult-to-flush areas, eventually leading to a flow disruption the equipment cannot compensate for. And even if these objects make it through the equipment, they will end up on your parts and may cause paint defects.
To solve this, a fluid filter should be installed in your lines, ahead of the proportioner. A 100-mesh filter is the most commonly recommended size and will be adequate in most cases. A finer mesh may be required with more sensitive processes, or if smaller flowmeters are being used in your process. A high-quality fluid filter will have minimal pressure drop and can be added to most systems without additional changes. For a fully automated system, pressure transducers can be installed before and after the filter to measure pressure drop and indicate when the filter needs to be cleaned or replaced.
Eliminating Moisture in the Lines
Many catalysts and hardeners on the market today are extremely moisture-sensitive, especially isocyanates. When these materials interact with any moisture, they form hardened crystals that will damage seals and lead to valve failures. The most common sources of this moisture are from the supply air or the ambient air. Moisture in the supply air lines should be eliminated with a high-quality air dryer, and the operation of these dryers should be checked regularly. With regards to the fluid lines, whenever possible, leave the lines full of either solvent or catalyst, especially if the equipment is not going to be used for an extended period. If the lines are emptied, humidity in the air will cause crystallization with any leftover catalyst as the equipment sits.
Never Mixing Incompatible Materials
To reduce cost and system complexity, it is a common request to run as many coatings as possible through a single proportioner. However, it is critical to ensure all the desired coatings are compatible with each other. In general, the major coating types, such as epoxy, urethane, and acid-catalyzed, should never be run through the same proportioner. Even very small amounts of the materials will react with each other, creating sediment and crystals that will rapidly clog your equipment. Even proper flushing is usually not enough to completely prevent cross-contamination and the resulting clogging. As such, it is always recommended to run incompatible materials through separate circuits or separate pieces of equipment.
Proper Flushing
Incomplete flushing of your proportioner during color changes can result in both cross-contamination that may affect your finish quality, as well as insufficient removal of sediments and other particulates. The resulting build-up will increase after each color change, eventually clogging the equipment or packing-out the flowmeter. To ensure proper flushing, there needs to be enough solvent pressure, and enough solvent pushed through the system. Thicker coatings will need higher solvent pressures for a complete flush. To ensure you are using the correct amount of solvent each time, consider installing a solvent flowmeter on your proportioner. This will help you track your usage for consistency, as well as automate VOC reporting. Finally, ensure you are using a high-quality solvent with no water content, to avoid crystallization in the lines.
By implementing the best practices above, you can improve the performance of your system and reduce downtime.
About the Author
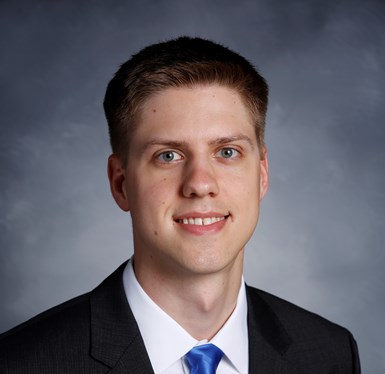
Jacob Fortmeyer
Jacob is a global product manager for Carlisle Fluid Technologies. Visit carlisleft.com.
Related Content
A Chromium Plating Overview
An overview of decorative and hard chromium electroplating processes.
Read MoreAnodizing for Bonding Applications in Aerospace
Anodizing for pre-prep bonding bridges the gap between metallic and composite worlds, as it provides a superior surface in many applications on aluminum components for bonding to these composites.
Read MoreHow to Maximize Nickel Plating Performance
The advantages of boric acid-free nickel plating include allowing manufacturers who utilize nickel plating to keep up the ever-changing regulatory policies and support sustainability efforts.
Read MoreAlkaline Cleaning Guide
Gregg Sanko, Senior Chemist, Oakite Products, Inc. provides an overview of the alkaline cleaning process.
Read MoreRead Next
Adjusting Viscosity in Liquid Coatings
Mike Bonner of Saint Clair Systems discusses the problems that can arise from adding solvents to liquid coatings to adjust viscosity.
Read MoreCan a Flawless Liquid Coating Finish be Achieved?
What are the best practices to achieve a flawless liquid coating finish? J.B. Haydell from Accudraft shares the details on avoiding dust, debris and other contaminants while spraying.
Read MoreSwitching to Rotary Atomization
Justin Hooper of Carlisle Fluid Technologies offers a review of rotary atomizer technology and discusses what to keep in mind when considering rotary atomizers.
Read More