SurfTec Receives $1.2 Million Award to Develop Novel Coating
Beckford and Zou discovered a novel approach that significantly improved wear resistance of PTFE coatings, which are applied to the surfaces of tools and cooking wear to reduce friction and adhesion.
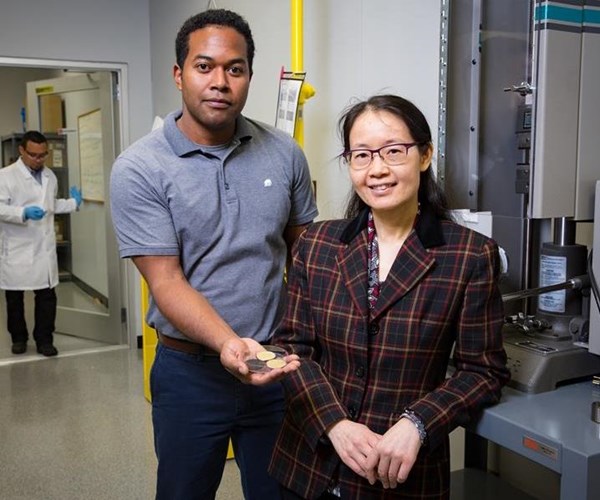
SurfTec CEO Samuel Beckford and Min Zou.
The U.S. Department of Energy awarded $1.2 million to SurfTec LLC, a company affiliated with the University of Arkansas Technology Development Foundation to continue developing a nanoparticle-based coating to replace lead-based journal bearings in the next generation of electric machines.
SurfTec is located at the Arkansas Research and Technology Park, and was founded by Samuel Beckford and Min Zou, professor of mechanical engineering. Beckford, while a graduate student at the UA, and Zou discovered a novel approach that significantly improved wear resistance of polytetrafluoroethylene (PTFE) coatings, which are applied to the surfaces of tools and cooking wear to reduce friction and adhesion.
For the past six years, researchers in Zou’s laboratory and, more recently, at SurfTec, have refined and tested a solid lubricant coating – a thinner and more durable PTFE – to reduce friction and wear in manufacturing equipment. Beckford said testing has demonstrated that SurfTec’s coating compares favorably to standard solid lubricant coatings used by industry.
Journal bearings are mechanical devices meant to reduce friction between the surfaces of moving parts in machine components. The U.S. Department of Energy is specifically interested in new products that can reduce friction in high-speed, medium-voltage electric motors and generator systems. Beckford said that about half of all electric motor problems and breakdowns are due to bearing failures. Also, to improve reliability and reduce negative environmental impact of lead-based bearing materials, industry and research groups have concentrated on developing new lead-free bearing materials.
“The use of low-friction polymer coatings on the surface of bearings is an attractive option to reduce friction and wear during start/stop or transient operation,” Beckford said. “Our coating could potentially address this problem, while also reducing costs, complexity and oil consumption.”
Successful integration of SufTec’s nanomaterial coating in journal bearings could reduce friction by 10 percent and increase the life of parts by 40 percent, Beckford said. If achieved, these outcomes would meet the Department of Energy’s goal of using lead-free bearings and reducing energy losses in high speed, megawatt class, electric motors and generator systems.
Information provided by the University of Arkansas; click HERE to read more
Related Content
-
Possibilities From Electroplating 3D Printed Plastic Parts
Adding layers of nickel or copper to 3D printed polymer can impart desired properties such as electrical conductivity, EMI shielding, abrasion resistance and improved strength — approaching and even exceeding 3D printed metal, according to RePliForm.
-
How to Choose Between Sulfate and Chloride-Based Trivalent Chromium
There are several factors to consider when choosing between sulfate and chloride-based baths for trivalent chromium plating. Mark Schario of Columbia Chemical discusses the differences and what platers should keep in mind when evaluating options.
-
How to Maximize Nickel Plating Performance
The advantages of boric acid-free nickel plating include allowing manufacturers who utilize nickel plating to keep up the ever-changing regulatory policies and support sustainability efforts.