Understanding Infrared Line-of-Sight
Marty Sawyer of Trimac Industrial Systems offers insights into using infrared to accelerate your powder coating curing operations.
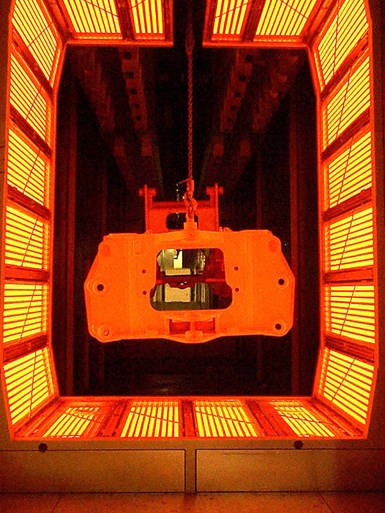
An infrared boost oven can accelerate the curing process so that less time in a cure oven is needed.
Photo Credit: Trimac Industrial Systems LLC
Q: I am considering using infrared for my process and I am concerned about line-of-sight issues. What exactly is this and is it an issue in a powder coating operation?
A: Great question! To understand line-of-sight, you first must understand infrared, which is basically light energy. It is part of the electromagnetic scale just below visible light. When you stand in the sun, you feel the line-of-sight energy of warmth. When you move to the shade, you feel the line-of-sight energy being blocked. In process heating, line-of-sight is the ability of the infrared energy to see the part. When a part has a complex shape, interior portions can be shielded from the light energy basically restricting the light from “seeing” all surfaces of the part, thereby creating a line-of-sight challenge.
If light energy cannot see all areas of the part, does that mean infrared will not work on anything other than a flat part? In theory that is correct because light cannot see around corners. However, in real-world applications, infrared can be used to heat and cure even complex weldments.
To get the benefits of infrared on a complex part, another part of heat transfer physics, conduction, plays a huge role. Conduction is transferring thermal energy through direct contact with matter. If you put a metal poker in a fireplace and leave it, the heat will “conduct” up the handle. Most commonly in powder coating, convection heat is used to cure complex shapes. The oven’s hot air does not bend around the corners of the part either, but the length of time allows conduction to help the part cure itself. The heat transfers via conduction into the hidden areas to cure anything the hot air cannot easily reach. With infrared, you can accomplish the same result on complex parts, only faster also through conduction. For instance, a gas catalytic oven is typically 3X faster than convection, but a complex weldment can still be cured through the assistance of conduction. With electric infrared, the process can be up to 10X faster than convection cures, however, the speed reduces the time for conduction to play a role as the part is not in the oven long enough.
Another consideration is how are you considering using infrared in your line? In a boost or gel application, it is typically not a major issue. The point of a boost is to accelerate the curing process so that less time in a cure oven is needed. The only way to speed conduction is through higher temperatures so a boost will drive more heat into a part much quicker than the convection oven can. Even if there are line-of-sight restrictions, the point is to accelerate conduction so those issues will typically be resolved in the cure oven. A boost or gel oven, though, still should be designed to ensure infrared energy coverage around the part to limit the line-of-sight issues. The better coverage you have, the less this will be an issue. If you are considering a cure application using infrared, line-of-sight can pose a bigger challenge. If the products are basically flat, you have no line-of-sight challenges, so cure is easily and quickly attained. If your parts have a complex shape, then your materials handling may be of assistance such as rotating the part in an overhead or chain-on-edge configuration. If the parts are not moveable, then you need conduction to also play a role. You still should be able to cure the product in about a third of the time vs. convection and possibly faster.
Another consideration affecting line-of-sight is infrared heater design. You would think the hotter the heater, the faster the process would work, right? Well, it’s a bit more complicated than that. Regardless of how much infrared energy you direct toward a part, what really matters is how much energy gets absorbed. Hotter is not always better because the energy is more likely to be reflected off the part vs being absorbed into it. The rate of infrared absorption of organic matter is in the medium to long wavelengths (300°F-1500°F). All infrared heaters emit infrared energy at their designed temperature/wavelength (temperature is inversely related to wavelength). For instance, gas catalytic emits in the 300°F-1,000°F range (long wavelength) and electric infrared is typically designed to emit at 800°F-4,000°F (medium to short wavelength). At the shorter wavelengths, the reflection of energy typically also goes up. If the energy only gets partially absorbed, then line-of-sight is even worse.
Bottom line, line-of-sight is an issue and must be part of the consideration in using infrared to accelerate your powder coating operation. To understand how it might affect your parts, you should work with an experienced infrared oven designer and have them perform tests in their lab. Using an oven temperature logger, the impact of the infrared energy on areas that might have line-of-sight issues can be probed for exact results. With data, you will know how infrared can be successfully incorporated into your line.
About the Author
Related Content
Trivalent Chrome Overview
As the finishing industry begins to move away from the use of hexavalent chromium to trivalent chromium, what factors should finishers consider as they make new investments? Mark Schario, chief technology officer for Columbia Chemical offers a helpful overview of this complicated topic.
Read MorePrevent Plating Problems with Critical Inspections
Tanks and their contents should be regularly inspected visually and analytically. When a quality issue arises, it is important to quickly pinpoint where the main problem is by checking which parameter is out of line.
Read MoreHow to Address Declining Powder Coating Coverage Over Time
Fine particles from reclaim could be to blame for powder coating problems that emerge over time. Avoid problems by keeping hooks clean, maintaining guns and using reclaim powder quickly to avoid accumulation of fines.
Read MoreUnderstanding and Managing White Spots on Anodized Aluminum
Having trouble with spotting defects when anodizing? Taj Patel of Techevon LLC offers a helpful overview of the various causes of white spots and potential solutions.
Read MoreRead Next
A ‘Clean’ Agenda Offers Unique Presentations in Chicago
The 2024 Parts Cleaning Conference, co-located with the International Manufacturing Technology Show, includes presentations by several speakers who are new to the conference and topics that have not been covered in past editions of this event.
Read MoreEducation Bringing Cleaning to Machining
Debuting new speakers and cleaning technology content during this half-day workshop co-located with IMTS 2024.
Read MoreDelivering Increased Benefits to Greenhouse Films
Baystar's Borstar technology is helping customers deliver better, more reliable production methods to greenhouse agriculture.
Read More