Valence Expands Titanium, Hard Metal Processing To All 10 U.S. Locations
Valence’s titanium and hard metal processes include titanium etch/pickle; passivate; phosphate fluoride; alpha case removal; high-temperature stress relieve; sol gel; and abrasive blast, among others
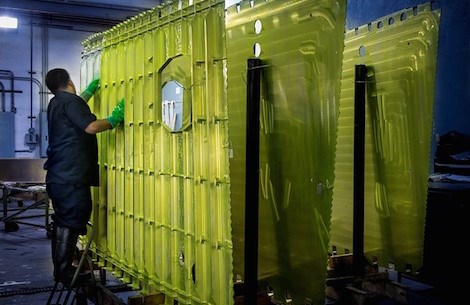
Valence Surface Technologies, one of the largest independent surface treatment company in the U.S., announced it now offers titanium and hard metal processing at each of its 10 facilities located throughout the U.S.
Recently, several Valence facilities added and enhanced their hard metal service offerings, solidifying Valence as the largest titanium and hard metal processor for the aerospace and defense industries.
“At Valence, our goal is to take the hassle out of special processing and allow our customers to focus on their core competencies,” said Valence CEO Tracy Glende. “As titanium content has increased on aerospace programs, our customers have asked for added capacity and redundancy of capabilities across the country, and Valence has responded. With our expanded capabilities, Valence will improve the supply chain for large envelope, high intrinsic value titanium and hard metal parts.”
Valence’s titanium and hard metal processes currently include: titanium etch/pickle; passivate; phosphate fluoride; alpha case removal; high-temperature stress relieve; sol gel; abrasive blast; shot peen; zinc spray; penetrant inspection; mag particle inspection; and primer and topcoat.
Specific processes added to particular Valence facilities include:
-Eastman, Ga. facility – As part of a major capital expansion project, Valence added a 25-foot titanium processing line with capabilities for non-destructive testing, titanium clean and pickle, sol gel and paint including bond primer. The large envelope tank line will support long parts such as helicopter blades, abrasion strips and structural airframe parts. The line has been installed and will be placed into service by the end of October 2015. The Eastman site has added prime approvals to support growing programs including the Boeing 787, Sikorsky UH60 Blackhawk and the Bell 525 Helicopter.
-Carson, Calif. facility – Valence’s Carson site has expanded its titanium capabilities to support large envelope, high-value structural aerospace and space parts. Carson has enhanced its nondestructive testing (NDT) line, added new 27-foot titanium etch/pickle capability, and installed new titanium abrasive-blast capability up to 30 feet. In addition, the Carson site has added key approvals to support growth in the A350, JSF, 787 and 737 max programs.
-Everett, Wash. facility – Valence added titanium processing and expanded its steel capabilities at its Everett location in response to increasing demand and current constraints in the Pacific Northwest supply chain. Included in the expansion is a new large envelope shot peen pass-through cabinet and a new 12-foot titanium clean and pickle and passivate line, which will be operational in Q4 2015. In addition to its current aluminum and steel capabilities, Everett now offers shot peen, sol gel, titanium clean and pickle, and paint for titanium. Everett is adding Boeing approvals in 2015 and will be adding Airbus approvals in 2016.
Related Content
-
Corrosion Protection Options for Aluminum
Seeking to understand aluminum corrosion and prevention? Jacob Weingart of Columbia Chemical offers a helpful overview of corrosion protection options for aluminum and its alloys.
-
NADCAP Shop Digitizes to Eliminate Paper Trail
Customizable ERP software has transformed a 27-year-old manual metal finishing job shop into a state-of-the-art paperless company with full digital traceability in about 10 months.
-
Trivalent Chrome Overview
As the finishing industry begins to move away from the use of hexavalent chromium to trivalent chromium, what factors should finishers consider as they make new investments? Mark Schario, chief technology officer for Columbia Chemical offers a helpful overview of this complicated topic.