When to Introduce Automation Into Your Finishing System
Looking to increase productivity for your liquid coating operation? John Owed of Carlisle Fluid Technologies provides examples of how automation can help improve quality and efficiency for paint spray equipment.
Q: We currently apply decorative finishes for a wide range of components for high-profile customers. We utilize masks to shield certain areas of the parts and manual spray equipment to coat the designated areas. Production and quality requirements are increasing, and we are challenged with finding qualified painters. What options exist for automating our process?
A: For your specific application, there are some very well-designed compact solutions that utilize robotic spray. These systems typically consist of a spray booth, a six-axis robot with application equipment, and an indexing or shuttle table. The operator loads parts into a fixture complete with mask onto the table; the part is then shuttled in front of the robot and coated. The part shuttles back out, and the operator removes it and reloads. Depending on your production requirements and part complexity, multi-position tables can be provided so that one part is being coated and the next is being loaded.
Since you are removing the operator from the point of application, ensuring that you have high-quality spray equipment and repeatable fluid delivery, and air management equipment is critical. In most instances, these parameters can be fully interfaced through the robot controller and stored along with the path program based on part style, allowing for repeatable results and overall improvement in quality.
Q: We are coating small gas cylinders supported on a spindle conveyor system and rotating through the spray booth. We use three HVLP guns with basic controls in the spray booth to coat the cylinders. We recently had a third-party company measure our paint utilization and were shocked to discover that we are only 23% efficient with our application. What can we do to improve the efficiency of our application?
A: You note “basic controls,” so I assume that the spray guns are on continuously. One immediate improvement that you can make to improve your transfer efficiency (TE) would be to add an automated triggering system. This triggering system would utilize a photo eye outside the spray booth to detect part presence and width. This information would be used to turn the spray guns on and off based on the part presence and trigger the applicator off in between the parts.
For instance, if your parts are on 9-inch spindle centers but only 6 inches wide, that means you have a 3-inch gap in-between the parts where the guns are staying on. By shutting the guns off with an automatic triggering system, you would reduce your total material usage by 1/3; this would improve your existing TE to approximately 34%, which is in the lower expected range for HVLP spray in this type of application.
If you want to improve your TE drastically, I suggest upgrading to electrostatic applicators. With electrostatic applicators, a negative high-voltage charge is introduced at the point of atomization. The charged atomized particles are then attracted to the grounded part being sprayed. This reduces the amount of overspray and allows for a more uniform and efficient application. Both air-atomized and rotary atomizers are available. In many situations, using electrostatic applicators, you can double your TE or cut your material usage in half.
You should contact a reputable equipment supplier and utilize their applications lab to configure an application solution based on your coating, parts, and process requirements. By increasing your transfer efficiency and reducing your coating usage, you can typically justify a quick return on investment to pay for the equipment upgrades in less than six months. You will also significantly reduce your filter changes, maintenance, and waste disposal cost.
About the Author
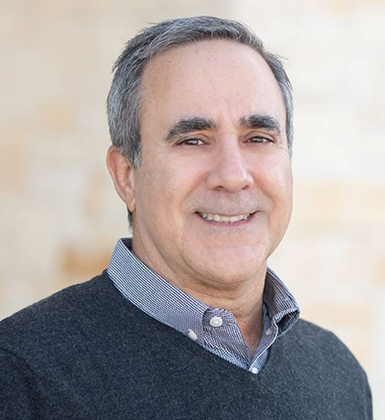
John Owed
John Owed is the finishing SBU director at Carlisle Fluid Technologies. Visit carlisleft.com
Related Content
How to Choose Between Sulfate and Chloride-Based Trivalent Chromium
There are several factors to consider when choosing between sulfate and chloride-based baths for trivalent chromium plating. Mark Schario of Columbia Chemical discusses the differences and what platers should keep in mind when evaluating options.
Read MoreHow to Maximize Nickel Plating Performance
The advantages of boric acid-free nickel plating include allowing manufacturers who utilize nickel plating to keep up the ever-changing regulatory policies and support sustainability efforts.
Read MoreUnderstanding and Managing White Spots on Anodized Aluminum
Having trouble with spotting defects when anodizing? Taj Patel of Techevon LLC offers a helpful overview of the various causes of white spots and potential solutions.
Read MoreRead Next
The Solution to Costly Aircraft Paint Adhesion Failure
Lucas Dillingham, of surface inspection technology provider Brighton Science, offers insights for avoiding aircraft paint defects and adhesion failures.
Read MoreHow to Avoid Mud Cracking
Julie Holmquist of Cortec Corporation discusses ways to avoid mud cracking defects when applying anticorrosion coatings.
Read MoreThe Importance of Benchmarking Your Application Parameters
Having repeatability issues in your coating process? John Owed of Carlisle Fluid Technologies discusses the importance of benchmarking your application parameters in order to identify and quickly resolve problems.
Read More