Nissan Launches New Manufacturing Initiative
Lower-temp curing paint and post-paint robotic inspection are part of it.
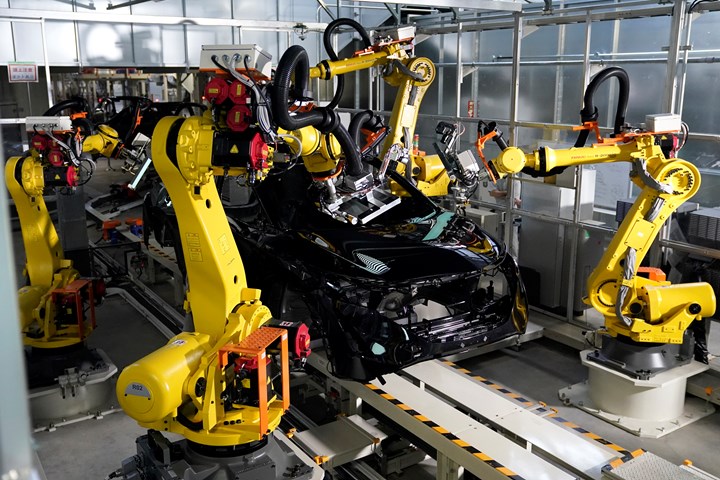
The paint line at the newly launched Nissan Intelligent Factory at the vehicle manufacturer’s site in Tochigi, Japan. Objectives are energy savings, high quality and addressing a labor shortage caused by an aging society. Photo Credit: Nissan
Nissan Motor Corp. (as in the overall organization) is undertaking a transition of its manufacturing operations as it works to create factories that are accommodating for workers of various types, help achieve zero-emissions, and utilize robots to enhance production quality.
It is called “Nissan Intelligent Factory.”
The first implementation went into production the first week of October at the company’s Tochigi Plant in Japan, where the company’s Ariya electric crossover is being produced (it is presently in pre-production).
Not surprisingly, there is a proliferation of robots performing tasks ranging from installing headliners to adjusting suspension links to within 0.1°.
In the paint shop, they’re using a newly developed water-based paint that is robotically applied. One interesting aspect of the paint is that it cures at a temperature that allows bodies (metal) and bumpers (polymer) to be put in the same oven, thereby reducing energy consumption by 25%.
Also in the paint booth, there is a dry powder that absorbs any paint mist so that the collected material can be reused.
What’s more, they’re recycling the air in the paint booth, for a 25% energy consumption savings there.
After the body is painted, 11 robots are used to perform 100% inspection of the body and the bumper. The system can detect dust and debris 0.3 mm in diameter. Inspection results are uploaded to a centralized management system that (1) allows human inspectors to check results with a smart phone and (2) provides traceability for each vehicle.
The Tochigi Plant is just the start. “By rolling out the Nissan Intelligent Factory initiative globally, starting at the Tochigi Plant, we will more flexibly, efficiently and effectively manufacture next-generation vehicles for a decarbonized society. We will also continue to drive innovation in manufacturing to enrich people's lives and to support Nissan's future growth,” said Hideyuki Sakamoto, Nissan’s executive vice president for manufacturing and supply chain management.
There is one interesting reason why Nissan chose the Japan location for the launch (beside the fact that Tochigi is about 90 miles north of Yokohama, where Nissan is headquartered).
According to Nissan, “the business environment surrounding manufacturing is undergoing major changes. In Japan, there is a need to break away from conventional labor-intensive manufacturing to cope with an aging society and serious labor shortage.”
When you don’t have people to do the work, it is essential to figure out how to get robots to get the work done.
Related Content
-
Concrete Reinforced Bars Built to Last
Not all corrosion-resistant materials for infrastructure are created equally. Epoxy-coated steel rebar has advantages that other materials used to prevent corrosion do not.
-
Intumescent Coating Provides Up to 3 Hours of Fire Protection
PPG Steelguard 951 coating is designed to provide protection against fire and corrosion.
-
TTX’s Automated Conveyor Carrier System Offers Wireless, Flexible Operation
ACC system designed for reliable, consistent point-to-point movement of everything from small to heavy parts.