Dürr Launches Modular, Sustainable Spray Booth for Automotive
Dürr’s EcoProBooth boxes can transform individual painting lines into an efficient and flexible painting environment. The size and design of the box are standard, meaning straightforward conversions and extensions are possible without affecting production in other box segments.
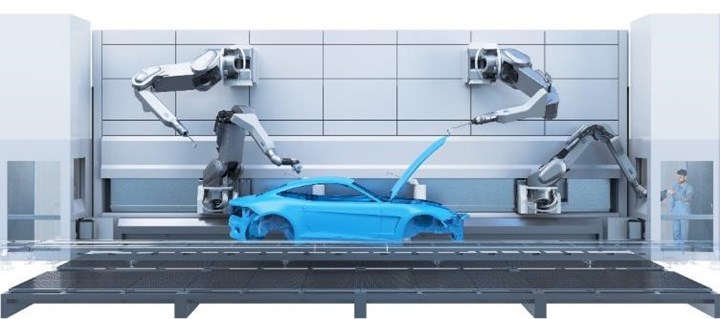
The service cubicles provide a constant supply of fresh air, which contributes to uninterrupted operation of the system. Photo Credit: Dürr
Dürr has introduced its EcoProBooth, a new spray booth technology designed for car manufacturers. EcoProBooth offers a modular box concept, independent lines and the combination of interior and exterior painting in a single box, which the company says enables scalability and flexibility previously only possible for small-scale series. Dürr claims the EcoProBooth can reduce carbon emissions and energy consumption by around 40% compared to current line concepts with dry separation. For existing systems that will continue to operate with wet scrubbing, the savings are projected to increase to 75%.
According to Dürr, EcoProBooth boxes can transform individual painting lines into an efficient and flexible painting environment. Each line features one position for all base coat applications and one for all clear coat applications. Fourteen zones become ten boxes, and each line can be individually controlled and brought online or offline as needed. In addition, subdividing the line into shorter segments minimizes color changes, saves paint and flushing agent and reduces costs and volatile organic compound emissions.
EcoProBooth cuts down on cycle time losses due to the booth’s ability to paint all standard passenger car types — from compact cars to SUVs. The size and design of the box are standard, meaning straightforward conversions and extensions are possible without affecting production in other box segments. The modular concept has also enabled Dürr to reduce the booth area.
In Dürr’s layout of future paint shops, two rigid lines will become five parallel EcoProBooth lines.Photo Credit: Dürr
A further factor in the uninterrupted operation of the system is the service cubicles located in the corners of the booth, which have a continuous flow of fresh air through them. Employees can safely access them without a breathing apparatus to clean or do minor servicing tasks on atomizers and tools while painting continues. In addition, the new EcoBell4 Pro Ux universal atomizer reportedly ensures that only four painting robots are needed per box. Dürr says that integrating all the painting tasks into one box eliminates the time required to convey bodies between the process steps for interior and exterior painting when the robots are inactive.
The EcoProBooth has a highly recirculated air rate due to its low energy needs with a ratio of recirculated air to fresh air of 95:5. According to Dürr, this means the process air is supplemented with 5% fresh air, taken directly from the clean room without any further air supply systems. The box also features overspray separation with the latest generation of the EcoDryScrubber. Once the paint particles have been removed from the air, they are reconditioned in a recirculating air unit assigned directly to the painting booth, which the company says reduces energy consumption and cost.
Dürr | durr.com
Related Content
-
Titrations: To Automate or Not to Automate?
What considerations should you keep in mind for automatic titrations? Conor McAnespie of Hanna Instruments discusses the benefits of auto titrators.
-
Tin and Tin Zinc Overview and Growth
Brett Larick of Columbia Chemical discusses the increasing demand for conductive finishes driven by the increasing electrification of vehicles.
-
Indonesian Plater Finds Fast Success in Auto Market
This father/son team, inspired by inventor Michael Faraday, focuses on anti-corrosion methods and automated processes to help their Indonesian plating business flourish.