Asterion’s Carbo-Dry Reduces Carbonates, Avoids Shutdowns
Skid-mounted system produces almost solid crystals for removal.
Reducing sodium carbonate in alkaline plating solutions is a continuous problem and, when not addressed, leads to issues with quality and plating efficiency. Sodium carbonate naturally results from the exposure of sodium hydroxide to carbon dioxide. The production of carbonates reduces the solubility of the metals required for cost effective plating, and can cause unnecessary use of proprietary additives to mask the problem.
Asterion, a surface technology company based in Indianapolis, introduced Carbo-Dry as a solution to carbonate build-up.
Asterion President Blair Vandivier says the Carbo-Dry unit offers a unique system for reducing carbonates utilizing a simple and relatively maintenance-free skid mounted system.
“Traditional methods for reducing these salts in solution involved removing the actual plating solution from the production line and freezing out the carbonates,” Vandivier says. “That meant shutting down the production line and pumping out the solution and placing it in an environment with temperatures that would allow the carbonates to drop out of solution. The remaining solution had to be separated from the remaining sludge and returned to the plating tank.”
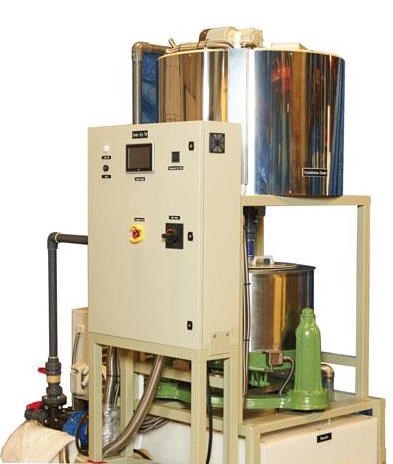
People have used this manual method to remove carbonates from plating baths for years, and Brent Burleson, Asterion’s director of national accounts, says that, while generally these processes are effective in reducing accumulated carbonates, there were quite a few problems that were an accepted part of the process.
“The Carbo-Dry automatically treats 50 gallons of plating solution in a batch process, producing roughly 70 pounds of crystal residue via a chill cycle,” Burleson says. “The sequence includes a centrifuge process that separates the plating solution from the carbonates."
The total cycle time in most cases is about three hours with a starting plating solution temperature of 80°F. Burleson says the treated solution is transferred back to the plating line, eliminating the need to shut down production or the need to have additional plating solution in reserve for continued operations during an off-line treatment.
The Carbo-Dry unit has a 4 ft. × 8 ft. footprint and is constructed of stainless steel and poly-propylene. There are relatively few moving parts which helps reduce maintenance costs.
For more information, call 800-428-0719 or visit asterionstc.com.
Originally published in the October 2015 issue.
Related Content
-
Products Finishing Reveals 2023 Qualifying Top Shops
Each year PF conducts its Top Shops Benchmarking Survey, offering shops a tool to better understand their overall performance in the industry. The program also recognizes shops that meet a set of criteria to qualify as Top Shops.
-
A Chromium Plating Overview
An overview of decorative and hard chromium electroplating processes.
-
Nanotechnology Start-up Develops Gold Plating Replacement
Ag-Nano System LLC introduces a new method of electroplating based on golden silver nanoparticles aimed at replacing gold plating used in electrical circuits.