Automated Coating for Complex Gear Components
Venjakob develops fully automated, compact robotic coating solution for complex gear components.
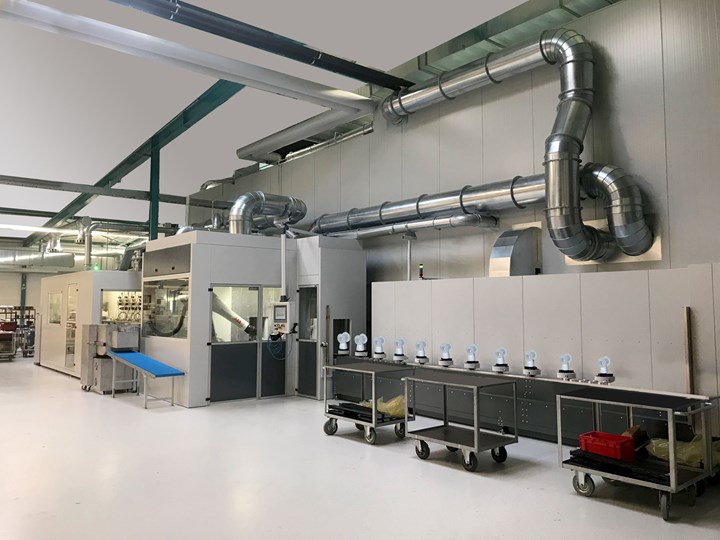
Fully automated and compact robotic coating solution for complex gear components.
Photo Credit: All photos copyright Venjakob
Fully automatic coating in serial production is part of many companies’ everyday operations. Order-specific production, on the other hand, is a different matter, because small batch sizes and the variety of parts requiring coating create significant challenges for the automation system. Venjakob has developed a system that permits fully automatic coating of complex gear components from a batch size of 1.
The components requiring coating are fully machined and pre-cleaned components for planetary and angular gears made of steel and aluminum. The varied range of components comprises 15 different gear types of different sizes. Measurements range from an exterior diameter of 50 mm to 350 mm, a length of 40 mm to 420 mm and a weight of 0.5 kg to 30 kg. The outer surface of the gear component requires coating.
Crucial controls and mechanical components
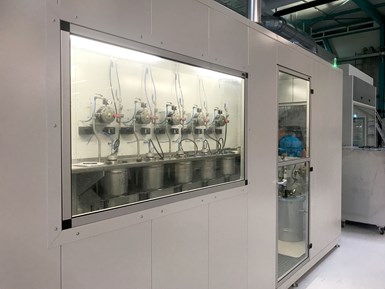
Paint supply system with integrated 2 K technology for 4 different color cycles.
“The particular challenge, in this case, was that the system had to be designed for batch sizes as low as 1 and had to adapt to different gear components automatically,” explains Kornelius Berg of Venjakob, who managed the project. “Each of these components got their own programs in the plant control system. They are differentiated by diameter, length, geometry, coating parameters and color. Once the component has been identified, the system selects the corresponding coating program and automatically completes the associated set-up.”
Component identification by bar code
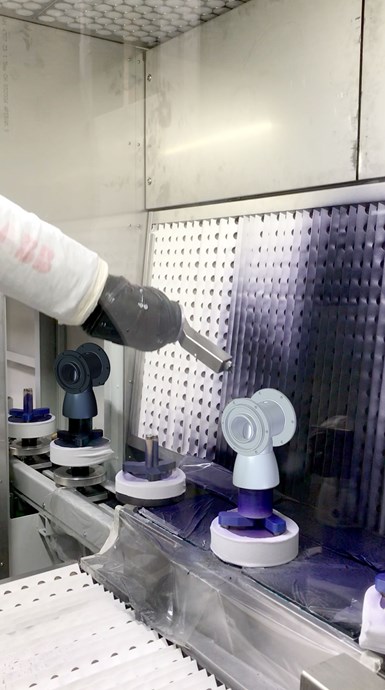
View into air-conditioned robot coating spray booth.
The only manual work involved is loading and removal. For each requirement, a suitable number of workpiece carriers is available, on which the machine operator can place the gear components with a jig for areas that should not be coated. It is not necessary to position the components in a specific way. “Everything was supposed to be quick and simple. In response to this request by the customer, we implemented suitable safety mechanisms,” Berg explains. After placement the operator scans the bar code of the gear component, the control system activates the associated coating program and pressing a release button starts the program. After release, the system automatically detects the position of the workpiece on the carrier. This means incorrectly positioned components can be detected. During this process, the system also checks whether the data transmitted by the bar code matches the workpiece dimensions. If the bar code does not match the component, the system immediately enters malfunction mode and signals the error. If the scanned bar code information matches the workpiece, the workpieces are transported through the coating process by a chain conveyor system in a clock-controlled manner.
After position detection, the workpieces are transported into the closed coating booth containing the coating robot. To ensure that a wide variety of gear parts (with and without connecting flanges), and rotationally symmetrical and asymmetrical parts, can be coated fully automatically with a spray gun, the coating robot was equipped with programs referred to as “master programs.” These programs are activated based on the component, taking the parameters into account. As previously described, the parameters are transferred to the control system when the bar code is scanned at the loading station. For the coating process this means that the coating speed or the coating angle of the spray gun are automatically adapted to the size and geometry of the gear part. Another important factor for consistently good coating results is the permanent air conditioning of the coating booth. The controlled air supply ensures that the temperature and air humidity are suitable for the coating process year-round.
Reduced material consumption
The system is designed for multiple coating materials. Venjakob engineers used a variety of approaches to keep the material consumption as low as possible. The coating material supply is positioned directly next to the coating booth in a closed ventilation and venting booth. As the system is used for coating gear components of different sizes, it is possible for e.g. only every second workpiece carrier to be filled. For this reason, a scanning unit checks whether or not the spindle is empty during entry into the coating booth. If the spindle is empty, the coating process is paused. Use of the coating robot permits targeted spraying. This already reduces overspray, but any overspray that still remains is collected by a filter system and can be reused.
Automatic cleaning of covers
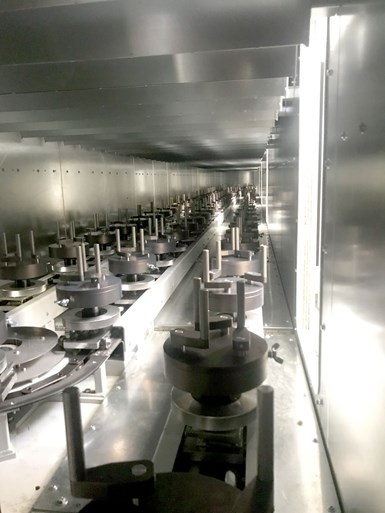
View into drying section with continuously variable temperature setting from 50-90°C.
After the coating process, the workpieces are first transported to the jig removal station. This station uses a horizontal and vertical axis system with grippers to remove the jigs that were put in place in the loading area and transport them to the cleaning station. Cleaning is performed in three steps: alkaline cleaning, rinsing with water, warm air drying. Then a conveyor belt returns the jigs to the loading area, where they can be reused.
The final important stations for the coating result are the evaporation channel and the jet drying channel. A removal point upstream of the evaporation zone was created for cases in which a coated workpiece is not supposed to pass through the dryer. Heavy workpieces can be removed with a crane at this point. Otherwise, the gear components on the spindles are first transported into the evaporation channel, then into the jet drying channel. In this section, the coating material is dried by recirculating air blowers. The temperature is continuously adjustable. The air humidity is kept at a consistent level. After the drying process, the now fully coated gear components are transported by the chain conveyor through the cooling channel and returned to the loading and removal area from the other end, in a manner of speaking.
A quantum leap of change
Where coating was previously performed manually in 3-shift operation, the fully automatic robot coating line with a spindle chain conveyor system achieves the same output in 2-shift operation, reducing both the cost of labor and of coating material while simultaneously ensuring consistently high coating quality. “The change from manual to fully automatic coating represents a quantum leap in this case,” Berg says.
Related Content
Henry Ford Is Still Right When It Comes to Color
Who would have imagined that more than 100 years after his famous statement about any color as long as it’s black would still have relevance of a sort?
Read MoreShedding Light on Surface Inspection
State-of-the-art reflector-based lighting system improves luminosity and ergonomics for surface inspection tasks while reducing energy usage.
Read MoreSurface Prep Solution for Rusted Rebar in Concrete
Julie Holmquist of Cortec Corporation discusses passivating corrosion on rebar and other reinforcing metals.
Read MoreConcrete Reinforced Bars Built to Last
Not all corrosion-resistant materials for infrastructure are created equally. Epoxy-coated steel rebar has advantages that other materials used to prevent corrosion do not.
Read MoreRead Next
Delivering Increased Benefits to Greenhouse Films
Baystar's Borstar technology is helping customers deliver better, more reliable production methods to greenhouse agriculture.
Read MoreA ‘Clean’ Agenda Offers Unique Presentations in Chicago
The 2024 Parts Cleaning Conference, co-located with the International Manufacturing Technology Show, includes presentations by several speakers who are new to the conference and topics that have not been covered in past editions of this event.
Read MoreEpisode 45: An Interview with Chandler Mancuso, MacDermid Envio Solutions
Chandler Mancuso, technical director with MacDermid Envio discusses updating your wastewater treatment system and implementing materials recycling solutions to increase efficiencies, control costs and reduce environmental impact.
Read More