Character Matters in Mechanical Finishing
How physical characteristics of vibratory bowls affect processing efficiency.
The operating channel of a traditional vibratory bowl is toroidal in shape. Parts to be refined are placed into the machine’s channel, along with the processing media of choice. During machine operation, parts roll within the channel and make laps around the machine’s center hub. A combination of the vertical rolling motion and horizontal sliding motion results in a helical motion path.
Machine manufacturers have adapted a number of engineering elements into machine design to increase the machine’s functional performance and operator ease, especially during unloading while increasing the efficiency of part processing. Physical characteristics that can be customized at the time of a machine build include the durometer value of the lining, the presence of OD wall ribbing, the shape of the machine’s walls, the presence or absence of a part unloading ramp and the use of a sound cover.
How do design characteristics affect machine performance? What should be considered when ordering a machine?
Polyurethane Liners
Vibratory bowls are outfitted with hot-poured polyurethane liners. The durometer hardness of the liner is an oft-cited machine characteristic. For certain specialty applications, the durometry hardness can be specified by the purchaser at the time an order is placed for the machine.
Durometer hardness is the measure of an object’s ability to resist indentation by a probe that is pressed into its surface using a prescribed load. The technique was developed by Albert Shore in the 1920s2.
Durometry is the principle technique used to quantify the hardness of assorted gels, elastomers and rubbers. While a Rockwell hardness tester is used to determine the hardness of a metal specimen, a durometer is used for measuring the hardness of gels, plastics and elastomers.
Durometer hardness is measured using a durometer tester, which uses a spring to depress an indentor pin into the surface being measured. The spring has been calibrated to apply a specific load of force with every test. The softer the surface being measured, the further the indenter pin can deflect the surface1.
Since the spring applies the same load force with each measurement, the differences in surface deflection between surfaces of varying hardness can be compared with a known measurement value1,2.
Indentor pins of varying widths and shapes are used for the different hardness range scales depending upon the hardness of the substrates to be measured2. For example, a sharp-pointed pin is unsuitable for a gel-like substrate because it would penetrate rather than deflect the surface when the measurement is made2.
Likewise, the indentor spring used for a harder substrate measurement varies across the hardness scales. A more robust spring is used to measure Shore A versus Shore 00 surfaces and a more powerful spring is employed for Shore D measurements2.
The unit of measure for the hardness reading is known as Shore Hardness, honoring Albert Shore. Different Shore Hardness scales are used for substrates in different hardness ranges. The most commonly used scales are the Shore 00 Scale for gels, the Shore A Scale for rubbers and Shore D Scale for plastics.
Liner durometry is also a consideration when sending a legacy piece of equipment out for relining. Relining vibratory equipment is an expensive proposition and the durometry hardness specified should correlate to the intended processing application.
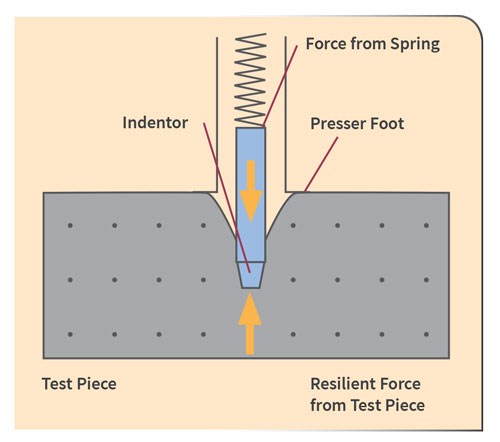
In operation, the indentor pin deflects the surface. The softer the surface, the deeper the penetration and corresponding deflection.
Polyurethane Liner Wear
Polyurethane liners are subject to wear and degradation as a function of machine usage. The more hours of operation or the more abrasive the media used, the more wear on the liner6.
Thickness of the polyurethane liner is manufacturer-specific. Higher-end equipment is typically supplied with liners with a thickness of 20 millimeters, approximately 0.80 inches. On the other end, more frugally priced equipment comes with liners having a thickness of 13 millimeters, approximately 0.50 inches.
As expected, the life of the vibratory equipment, whether vibratory bowl or vibratory tub, is substantially longer than the life of the machine’s liner. At some time during long-term machine ownership, the equipment will have to be relined.
Relining is an expensive proposition, but is less costly than the purchase of a new piece of equipment. The cost to reline a vibratory unit can vary between $3,000–$10,000 depending upon the size and complexity of the channel. Additionally, relining is accomplished off-site, resulting in additional shipping costs and ancillary production downtime while the equipment is absent during the relining work6.
It is beneficial to run the equipment practically to optimize the life of the liner. In generic deburring applications, abrasive ceramic media is used to mechanically scour the surface of parts being processed. The abrasive content of the media is integral to serve as the mechanical tool to impart deburring action and surface refinement. However, the abrasive in the media additionally abrades the machine liner. The more abrasive the media, the more aggressively it will wear the liner6.
Table I: Durometer Comparison Table |
|||
0 |
A |
D |
Common Objects of Comparable Hardness |
10 |
|
|
Marshmallow |
20 |
|
|
Gel bicycle seat |
25 |
|
|
Chewing gum |
30 |
|
|
Footwear gel insole |
40 |
|
|
Glazing putty |
50 |
10 |
|
Racquet ball |
60 |
20 |
|
Rubber band |
65 |
30 |
|
Artist’s gum eraser |
70 |
35 |
|
Automobile door trim |
75 |
40 |
|
Rubber garden hose |
80 |
45 |
|
Pencil eraser |
85 |
50 |
|
Automobile tire tread |
90 |
60 |
|
Vibe bowl rubber liner |
95 |
70 |
25 |
Plumbing fixture O-Ring |
100 |
75 |
30 |
Dress shoe heel |
|
85 |
35 |
Leather belt |
|
90 |
40 |
Vibe bowl polyurethane liner |
|
100 |
45 |
Hockey puck |
|
|
55 |
Shopping cart tire |
|
|
60 |
Ebonite bowling ball |
|
|
65 |
Golf ball cover |
|
|
70 |
Construction hard hat |
|
|
75 |
Football helmet |
Liner Replacement Costing
Using Table II, and knowing the bond number of the media being used makes it possible to project the overhead cost of liner wear as a function of vibratory equipment run time.
Wear Costing Example No. 16:
- A 20-cubic-foot vibratory bowl with a 0.8-inch thick, 90-durometer liner is being used.
- A 40-bond, ceramic abrasive media is used for deburring.
- The deburring cycle is 2 hours.
- Calculation Cost of Liner Attrition: (20 ft3)(2 hrs)($0.0600/hr/ft3) = $2.40
Wear Costing Example No. 26:
- A 20-cubic-foot vibratory bowl with a 0.8-inch thick, 90-durometer liner is being used.
- HDNA media used in chemically accelerated process cycle.
- Total accelerated chemical processing cycle is 2 hours.
- Calculation Cost of Liner Attrition: (20 ft3)(2 hrs)($0.0250/hr/ft3) = $1.00
Ribbed Versus Smooth
Ribbed liners are typically used in applications where small, flat parts are being processed. Rolling action in the vibratory bowl dictates that the parts rise along the OD wall, then plunge downward at the center hub. However, small, flat parts or media will adhere to the OD wall due to liquid surface tension and are removed from refinement time during the processing cycle. Media that adheres to the wall reduces the ratio of media to parts during the processing cycle, thereby retarding processing time. In such applications, the vibratory bowl should be constructed with a ribbed OD wall liner6.
Rubber Versus Polyurethane
In vibratory peen polishing operations, steel media is typically used to compressively flatten surface asperities. The average density of steel media is 300 pounds per cubic foot, though it varies slightly as smaller media packs tighter, yielding a slightly higher density per cubic foot of volume6.
During decorative peen polishing, asperities are not removed, but are bent-over and smashed flat onto the surface of the part to form a compressed layer of laminated asperity debris4. Since the asperities haven’t been removed during peen-polishing, the process is not used on parts that will be subjected to applied mechanical stresses such as bending, twisting or compressive loading because it would result in debris delaminating and the generation of mechanical failure initiation sites6.
Rather, peen-polishing is a finishing technique used on soft metals such as zinc, brass and copper to generate a cosmetically attractive final finish.
Steel media peen-polishing presents a unique complication in the vibratory bowl. As noted, the preferred and most typically supplied polyurethane liner has a Shore A 90-durometer hardness, a relatively hard surface. Likewise, the steel media used in peen-polishing is polished smooth and is dense at 300 pounds per cubic foot. Since a 90-durometer lining has little give, as detailed in Table I, the polished, heavy steel media mass will have difficulty gaining traction and will not roll in a bowl with a 90-durometer liner6.
The two opposing surfaces, the polished steel media and the 90-durometer liner, are both hard, inflexible and are slippery from the addition of a cleaning soap to the vibratory bowl. The result is that the steel media mass will slide horizontally, but will not roll vertically. Imagine a hockey slap shot propelling a puck on the surface of an ice rink; 100 percent sliding action with one hard surface meeting an opposing hard surface.
When steel peen-polishing, a Shore A 60-durometer hardness rubber is the preferred liner material. The weight density of the media mass above the lowest layer of media in the vibe bowl channel will indent the softer durometer rubber liner6,10. Thus, it momentarily forms a cup-like depression beneath the steel media. The momentary cup formation gives the steel media stable traction to initiate vertical rolling6.
Ramped-Channel Bowls
For convenience, it’s not uncommon to use a vibratory bowl equipped with a ramped-channel to facilitate part unloading and reduce time-consuming and laborious hand-unloading of a vibratory bowl.
In a flat-bottomed, or non-ramped vibratory bowl, the base of the operating channel is at a uniform depth beneath the OD rim, regardless of the location of a depth measurement. Beginning at the lowest point in the operating channel, the ramp rises around the center hub 360 degrees until it returns to its starting location. However, since it has risen during its lap around the hub, it is elevated above its lower starting point, creating a crest at the top of the ramp over which parts fall during processing.
During processing, a bridge is elevated so parts in the channel will continue to make laps around the bowl. During unloading, the bridge is lowered connecting the ramp to a separation deck. Media falls through holes in the deck back into the bowl’s operating channel. Parts will exit the far end of the separation deck into a judiciously positioned shop box6.
Although a ramp-equipped vibe bowl is a labor savings device, it must be used with some precaution due to the following operational characteristics6:
- Parts cresting the ramp fall on top of parts at base of the ramp.
- The channel depth, media volume decrease as ramp rises.
- Long parts cantilever ramp crest, bouncing forward until they fall.
- Parts on the separator deck bounce against one another as they cross the deck and exit the bowl.
Ramped Bowl Precautions
Parts cresting the ramp and falling atop parts in the lower portion of the ramp requires no explanation. This is an immediate potential initiation to part-on-part impingement damage. Therefore, ramped bowls are a better consideration when processing heat treated steel parts as opposed to softer metals such as zinc, aluminum, brass and copper. Heat-treated steel parts with final hardness values of Rc > 40 are more resistant to being damaged in such equipment6.
As the ramp rises in the bowl, the depth of the channel must decrease. The cross-sectional volume of media in any discrete location in the bowl is decreased as well. Media serves two purposes in vibratory processing: it refines the part and is the medium within which the parts are moving. Therefore, a specific ratio of media to parts is required to minimize part-on-part contact. As the cross-section channel volume of media decreases, induced by ramp climb, the protection from part-on-part contact is minimized as parts now are suspended amongst one another in a smaller media mass volume6.
When using a ramp-bottomed bowl to process long parts, the long configuration of the part will result in its extending or cantilevering over the ramp crest. Since the bowl is vibrating and the part is now separated from the media, it will bounce as it moves forward until sufficient length and weight cantilever forward, resulting in the part tipping over the crest6.
Depending on the amplitude of the machine and the metallurgical hardness of the part, the bouncing action will generate impingement damage along the edge of the part that is in contact with the ramp crest. Again, heat-treated parts of Rc > 40 are more forgiving in such applications6.
As explained, the rising ramp changes the media-to-part ratio resulting in a greater possibility of part-on-part contact damage. Nowhere is this characteristic taken to an extreme during vibratory processing, other than at the separator deck6.
The deck eliminates hand picking of parts by separating the parts from the media automatically during unloading. As media falls back into the bowl’s channel through holes in the separator deck, the parts are without the separation protection afforded by the media mass. This is a critical time during which part-on-part damage can occur. Soft metal parts such as zinc, brass, copper and aluminum are poor candidates for this unloading technique as they are easily subjected to impingement6.
Table II: Liner Wear vs. Media Bond |
|||
Media bond No. |
Media attrition rate in %/hr |
Liner wear cost1 in %/hr/ft3 of volume |
Run hrs. before reline required |
HDNA2 |
0.008 |
$0.0250 |
20,000 |
Porcelain |
0.100 |
$0.0250 |
20,000 |
10 bond |
0.130 |
$0.0350 |
16,700 |
20 bond |
0.350 |
$0.0415 |
13,750 |
30 bond |
0.750 |
$0.5000 |
10,000 |
40 bond |
1.200 |
$0.0600 |
8,350 |
50 bond |
2.000 |
$0.1000 |
5,000 |
60 bond |
2.750 |
$0.1075 |
4,650 |
70 bond |
3.500 |
$0.1538 |
3,250 |
XA3 |
4.000 |
$0.2000 |
2,500 |
1 $10,000 cost to reline 0.8"-thick lined 20 ft3 bowl |
|||
2 where HDNA = High Density Non-Abrasive |
|||
3 where XA = raw, lump, aluminum oxide |
Bowl Sound Covers
Two individuals standing next to a properly operating vibratory bowl can have a casual conversation and easily hear one another. However, a vibratory department may have dozens of machines operating simultaneously. Additionally, it is common to find that most vibratory bowls contain too small a mass of media. In such surroundings, the noise volume can increase and sound protection becomes desirable6.
Sound attenuation can be accomplished with a hard or soft sound cover. Hard-style covers are typically a clamshell design—sound absorbing foam lines a circular cover manufactured from either steel or fiberglass. The cover is raised or lowered by means of pneumatic pistons. The steel construction of such covers makes them robust and durable6.
Soft vibe bowl covers, also called bonnets, consist of sound-absorbing foam that lines a circular-shaped nylon cover that is suspended over the vibe bowl by an L-shaped flagpole and is raised or lowered by means of a clothes line rope. More economical, the bonnet-style sound cover affords the same degree of sound protection at a more budget-friendly price point6.
Both styles of cover serve their purpose well. Although the hard style machine is mechanically more robust, with proper care and use there is no longevity advantage or disadvantage to either style6.
Heat Retention
One word of caution when using a sound cover: when placed over the vibe bowl, the cover retains heat in the bowl that would otherwise have been atmospherically dissipated. As a result, the media mass within the vibe bowl becomes a heat sink and the liquid in the machine evaporates at an accelerated rate6.
The vibratory operator must remain aware that desiccation of the mass when using a sound cover is a distinct possibility. To prevent this from occurring, the flow rate of the soap compound going into the machine must be increased to a recommended level of 3 gallons per hour per cubic foot of volumetric mass6.
References
1. Albright Technologies, Leominster, MA; Image courtesy of Albright Technologies at info@albright1.com; 2015
2. Garratt, Alan; Shore Durometer History, 2006-2013, Image courtesy of website Atoms of June 5, 2014
3. Kitsch & Couture; Image courtesy of Rubylane, Charlotte, NC; 2015
4. Lette, W; Ploughing Apserity Tester; Image courtesy of University of Twente; Enschede, The Netherlands, 2015
5. Microdynamic Systems Laboratory; Image courtesy of Carnegie Mellon University, Pittsburgh, PA; Parts Feeders: Mobile Vibratory Feeder; 2015
6. Nebiolo, William P.; REM Training Manual Edition No. 9; 2014
7. Nuttall, Josh; How to Repair a Leaking Copper Pipe Fitting in a Water Line; Image courtesy of E-How at www.ehow.com; 2015
8. Oooh Shiny! Holley 94 Carb Polishing; Image courtesy of H.A.M.B. website; jalopyjournal.com; 2006
9. Riley Surface World; Image courtesy of Riley Industries Ltd., Aldridge, West Midlands, UK, online post; 2015
10.Rosler Metal Finishing U.S.A., LLC. 1551 Denso Rd., Battle Creek, MI 49015; 2015
11. Sweco, Inc.; Image courtesy of Sweco, Inc., 8029 Dixie Hwy., Florence, KY 41042; 2015
12. The LA Shop.com, Image courtesy of The LA Shop, 185 N. Sunset Ave., City of Industry, CA, 91744; 2015
13. Vibrochimica, SRL, Image courtesy of Vibrochimica, SRL, Via San Paolo della Croce, 2, Liscaste, Milano, Italy; 2015
14. Yacht Fittings Finished to a Very High Standard; Image courtesy of PDJ Vibro Ltd., 46 Barton Rd., Blatchley, UK
William P. Nebiolo is with REM Chemicals Inc. Contact him at bnebiolo@remchem.com, or visit remchem.com. Please visit PFonline.com to see all of the author citations in this paper.
Originally published in the February 2016 issue..
Related Content
Vulkan Blast Shot Technology
Vulkan Blast Shot Technology is a pioneer in the stainless steel abrasives market.
Read MoreCalculating Applied Media Force During Vibratory Finishing
What appear to be identically set-up vibratory bowls will finish identical loads of parts in varying time cycles. This paper offers a new technique to better predict what the operator will produce, by measuring the force applied to the parts. It is the efficiency of that force which controls the efficiency and speed of the refinement cycle.
Read MoreUnderstanding Shot Peening
A look inside shot peening — a process of “hammering” of work pieces with precisely defined blast media.
Read MoreHaving a Blast: Best Practices for Media Blasting
5 considerations for media blasting as surface preparation for coatings.
Read MoreRead Next
Education Bringing Cleaning to Machining
Debuting new speakers and cleaning technology content during this half-day workshop co-located with IMTS 2024.
Read MoreA ‘Clean’ Agenda Offers Unique Presentations in Chicago
The 2024 Parts Cleaning Conference, co-located with the International Manufacturing Technology Show, includes presentations by several speakers who are new to the conference and topics that have not been covered in past editions of this event.
Read MoreDelivering Increased Benefits to Greenhouse Films
Baystar's Borstar technology is helping customers deliver better, more reliable production methods to greenhouse agriculture.
Read More