Coatmaster Introduces Cloud-Based Measurement Tool
The Coatmaster Flex reportedly offers superior WiFi connectivity, an enhanced battery management system and fundamentally revised software which promotes greater process control and automation.
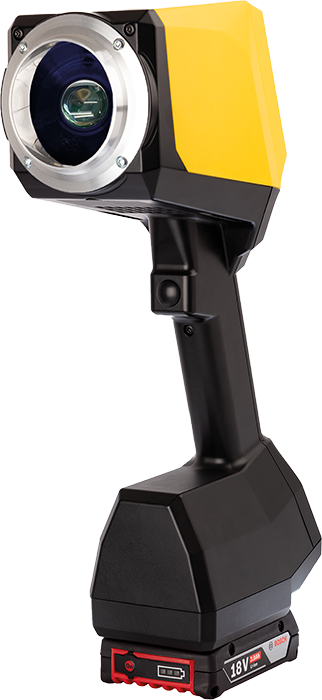
Coatmaster AG has announced the launch of its new, fully digital Coatmaster Flex for real-time non-contact coating thickness measurement that is optimally integrated into the production process.
According to the company, the Coatmaster Flex now offers superior WiFi connectivity, an enhanced battery management system and fundamentally revised software which promotes greater process control and automation. Its measuring process features SpectralBlue technology for disturbance-free operation.
The new WiFi module reportedly enables wireless connectivity with the cloud of up to 100 m range from the nearest access point; however, the capability to integrate and operate the device with a local server also remains an option. Meanwhile, the new battery management system enables more measurements to be taken with each individual charge.
The revised software includes automatic email notifications about the production process. In addition, new production tasks can be managed directly in the cloud, meaning that staff on the coating line only need to measure. Bi-directional communication with the coating lines enables new tasks to be automatically transmitted from the coating line to the Coatmaster Flex. Continuous information on the applied coating thickness is automatically synchronized with customers’ coating or ERP systems.
Andor Bariska, co-founder and co-CEO of Coatmaster AG, says, “By taking coating thickness measurement into the digital age, we are empowering the industry towards greater productivity and profitability with real-time information about their processes.”
Prof. Dr. Nils Reinke, co-founder and co-CEO of Coatmaster AG, adds, “Our quest has always been about enabling our customers to achieve greater economy, sustainability and ultimately profitability. The seamless embedding of non-contact coating thickness measurement in the production process is our central concern. We have created the optimal conditions for this with our open communication interfaces.”
Related Content
-
Mastering Uniformity Through Surface Prep Standardization
By standardizing surface preparation processes and adopting surface energy measurement, a company can achieve uniformity, quality and cost reduction.
-
NASF/AESF Foundation Research Project #121: Development of a Sustainability Metrics System and a Technical Solution Method for Sustainable Metal Finishing - 12th Quarterly Report
This NASF-AESF Foundation research project report covers the twelfth quarter of project work (January-March 2023) at Wayne State University in Detroit. In this period, our main effort concentrated on documenting technical content that was yet to be reported, including analysis of costs for specific technologies for sustainability improvement.
-
NASF/AESF Foundation Research Project #121: Development of a Sustainability Metrics System and a Technical Solution Method for Sustainable Metal Finishing - 15th Quarterly Report
This NASF-AESF Foundation research project report covers the twelfth quarter of project work (October-December 2023) at Wayne State University in Detroit. In this period, our main effort focused on the development of a set of Digital Twins (DTs) using the Physics-Informed Neural Network (PINN) technology with application on parts rinsing simulation.