Electrolytic Rack Stripping Best Practices
J.R. Eyerly of Haviland Enterprises discusses the benefits of switching to an electrolytic strip from a nitric-based nickel strip for rack stripping, as well as best practices to ensure desired results.
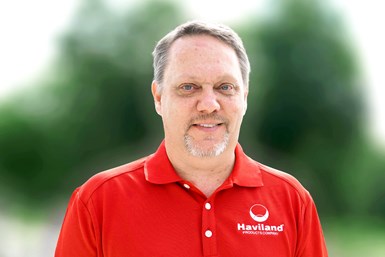
Eyerly
Photo Credit: Haviland
Q: We recently switched our nickel rack strip from nitric acid to an electrolytic rack strip for our nickel chrome process and we are experiencing attack on our stainless rack tips. Is this normal from this type of process?
A. One of the great benefits of an electrolytic rack strip over traditional nitric acid is a safer method of rack stripping without the dangers associated with the corrosivity of high concentrations of nitric acid. Electrolytic rack strips can remove nickel, as well as a variety of additional coatings including chrome, copper, zinc, cadmium, tin, and tin-lead solders. They are also beneficial in removing multi-layer deposits in one operation. Electrolytic rack strips are superior to basic nitric strips because of extended operating life and decreased attack on the plastisol rack coatings, which extends their life and reduces rack maintenance costs. In my experience, a properly maintained electrolytic rack strip will have removal rates of 1.5–2.0 mils in 5-10 min at 400 amp/ft2. A small amount of etching on 316 stainless steel tips is normal and after repeated use may become polished. Increased etch rates may be experienced with 301, 302, and 304 stainless while types 200 and 400 series are not recommended.
It is, however, important to maintain the solution within the manufacturer's recommended operating parameters to realize these benefits. These types of processes are typically proprietary and are offered by your plating chemistry supplier. While operating values may vary slightly by product, typical parameters are as follows:
-
Concentration (20%-30%)
-
pH Range (5.5–7.0)
-
Voltage (12-15 volts DC)
-
Anodic CD (300-600 amp/ft2) Current should not exceed 10 amps/gal
-
Cathode : Anode ratio (4:1 min)
-
Cathode : Anode Spacing (4-10")
-
Temperature (Ambient - 130ºF) Solution temperature will rise with normal operation. A heating source is typically not needed.
- Tank Construction: Steel lined with Koroseal, PVC, or rubber. Ensure tank design incorporates sufficient depth to allow for sludge accumulation.
Solution Control – Solution make-up and maintenance tends to be through a single component which is easily controlled through a wet titration procedure. Typical consumption rate is 1 gal/2,000-4,000 amp/hrs.
pH Control – Maintaining pH within the defined operating range is essential to reduce and/or eliminate chemical attack on stainless rack tips. As metal is removed the pH normally rises and may require the use of an additional proprietary additive to lower the pH of the solution. It is important to note that operating the solution below a pH of 5.5 will result in excessive attack of the rack tips.
Cathodes – Common cathode construction is 301, 304, or 316 stainless steels. Cathode to Anode ratio is typically 4:1 minimum with an anodic current density of 300-600 amp/ft2.
Switching to an electrolytic strip from a nitric-based nickel strip is one way to make your process safer, more versatile, and more robust. Monitor the bath for pH, concentration, and the size of the loads running through the bath, standardizing, if possible, to maintain the proper anode to cathode ratio. Regular line audits to monitor sludge formation around the anodes and within the tank will give you a visual indication of the solution performance.
If the pH is maintained within the recommended range, the process will not attack 304-316 type stainless rack tips. Periodic sludge removal will extend the life of the solution. Ensure cathode to anode ratio is a minimum of 4:1 to minimize excessive cathode current densities and include a routine inspection of the cathodes for sludge formation. Sludge formation on the cathode indicates an improper cathode to anode ratio and/or evidence the pH is operating higher than recommended.
About the Author
J.R. Eyerly
J.R. Eyerly is a technical sales representative at Haviland Enterprises Inc. Visit havilandusa.com.
Related Content
Liquid Chrome Vs. Chromic Acid Flake
Contemplating how to continue offering chromic acid services in an increasingly stringent regulatory world? Liquid chrome products may be the solution you’re looking for.
Read MoreAn Overview of Electroless Nickel Plating
By definition, electroless plating is metal deposition by a controlled chemical reaction.
Read MoreNanotechnology Start-up Develops Gold Plating Replacement
Ag-Nano System LLC introduces a new method of electroplating based on golden silver nanoparticles aimed at replacing gold plating used in electrical circuits.
Read MorePossibilities From Electroplating 3D Printed Plastic Parts
Adding layers of nickel or copper to 3D printed polymer can impart desired properties such as electrical conductivity, EMI shielding, abrasion resistance and improved strength — approaching and even exceeding 3D printed metal, according to RePliForm.
Read MoreRead Next
Addressing Problems With Carbon Treatment for Nickel Tanks
Getting defects after performing carbon treatment and maintenance? Josh Fish of Pavco Inc. offers insights for mitigating problems that might arise from carbon treatment for nickel tanks.
Read MoreBe Prepared: Managing Environmental Inspections
Is your shop ready for an environmental inspection? Preparation and documentation can help minimize your facility’s risk of noncompliance.
Read MoreImproving Leveling in Nickel Systems
Chad Murphy of Columbia Chemical offers insights for addressing issues with leveling in nickel systems.
Read More